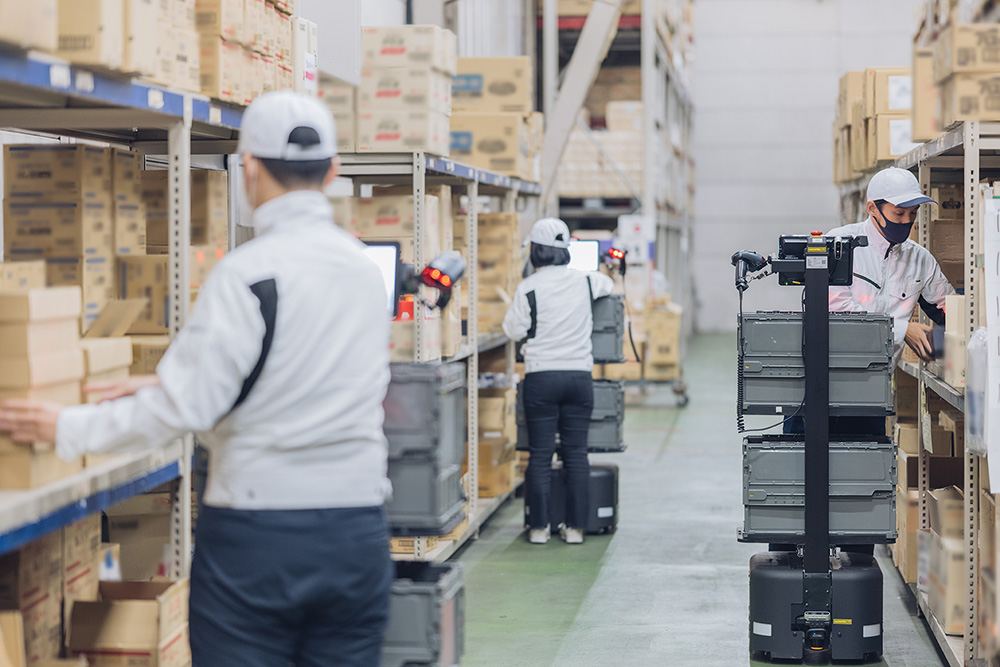
In today’s fast-paced warehouse environments, Autonomous Mobile Robots (AMRs) are not just becoming key players, but are actively transforming operations. Whether you’re a Warehouse Operations Manager, Director of Supply Chain, or an industrial engineer, understanding the key terms related to AMRs will help you stay ahead. These robots drive efficiency and flexibility, fundamentally changing how goods are moved, picked, and delivered within warehouses.
Essential Terms
This glossary covers some essential terms and concepts. It will help you optimize the use of AMRs in your daily operations and ensure you make informed decisions that align with the future of automation.
INDEX
Types of Robots
- Collaborative Robots (Cobots)
- Autonomous Mobile Robot (AMR)
- PA-AMR (Pick Assist Autonomous Mobile Robot) Pick-Assist Robot
- Automated Guided Vehicle
AMR Features and Technologies
- Obstacle Avoidance Technology
- LiDAR (Light Detection and Ranging)
- Simultaneous Localization and Mapping (SLAM)
- Payload Capacity
Common Types of Software Used in Warehouses
- Warehouse Management System (WMS)
- Warehouse Control Software (WCS)
- Fleet Management System (FMS) or Warehouse Execution System (WES)
- Enterprise Resource Planning (ERP)
Terms in Warehouse Operations Procedures
- ABC Classification
- Slotting
- Discrete Picking
- Batch Picking
- Wave Picking
- Zone Picking
- Order Line
- Lines Per Hour
- Units Per Hour
- Picks Per Hour
- Pick Module
Types of Robots
Collaborative Robots (Cobots)
Cobots are a subcategory of robots designed to work collaboratively and safely alongside humans, often in close proximity. Cobots can take many forms. Some cobots are fixed in place robotic arms with grippers. Some Autonomous Mobile Robots (AMRs) are cobots. Pick-Assist AMRs are a subset of Cobots. However, not all forms of AMRs are cobots. The key differentiating feature that makes a robot a cobot, is that cobots can interact directly with human workers safely. Cobots can assist with tasks such as transport, assembly, lifting, or precision work, complementing human efforts rather than replacing them.
Autonomous Mobile Robot (AMR)
Autonomy goes beyond simple automation. While traditional automated systems follow fixed, pre-programmed routes, AMRs are designed to make independent decisions on the go. They don’t need predefined paths or human intervention to navigate a warehouse. Instead, they rely on sophisticated sensors and mapping technologies to detect their surroundings and adjust their routes in real time. This allows AMRs to react to dynamic environments—avoiding obstacles, rerouting due to layout changes, or optimizing travel paths on the fly. In short, AMRs bring flexibility and adaptability to automation, enabling smoother and more efficient operations.
PA-AMR (Pick Assist Autonomous Mobile Robot) Pick-Assist Robot
A PA-AMR is a specialized form of Autonomous Mobile Robot (AMR) designed to work alongside human workers in the picking process, typically found in warehouses and fulfillment centers. These robots automate time consuming actions in the order-picking process, such as transporting goods from warehouse locations to packing stations. They can commonly be identified as having an onboard user interface providing instructions to associates. A PA-AMR will meet an associate in an aisle, display easy to understand and helpful instructions for what items to pick and from where, once the picking associate has put the items onto the robot, the robot will transport the items to the packing station. This collaboration between robots and humans enhances overall productivity, reducing the physical strain on workers and allowing them to focus on more complex tasks.Unlike AGVs, PA-AMRs can autonomously navigate the warehouse, avoiding obstacles and optimizing routes in real time. This combination of autonomy and precision ensures faster order fulfillment, fewer errors, and improved operational flow in dynamic warehouse environments.
Automated Guided Vehicle
Automated Guided Vehicle (AGV) is a type of robot that operates based on pre-programmed instructions or follows fixed, predefined paths. These robots are designed to perform specific, repetitive tasks with minimal human intervention, but they cannot make independent decisions or adapt to changes in real time. Automated mobile robots are effective in predictable environments where tasks and routes don’t frequently change, such as moving goods along set conveyor paths or shuttling items between defined points.
How and AGV Differs from an Autonomous Mobile Robot (AMR)
While both types of robots perform similar functions in material handling, the key difference is their level of independence. Automated Guided Vehicles (AGVs) are restricted to pre-programmed routes and rely on fixed infrastructures. AGVs may have obstacle detection, but might not have obstacle avoidance. Without obstacle avoidance, AGVs will commonly come to a stop, sound an alert and wait for the obstacle to clear or for further instructions. In contrast, Autonomous Mobile Robots (AMRs) can navigate dynamically, adjusting their routes based on real-time data and environmental changes. AMRs can operate with more flexibility, making them ideal for environments where layouts or tasks frequently change, whereas automated mobile robots are more suited to static, structured settings.
AMR Features and Technologies
Obstacle Avoidance Technology
This is a critical feature embedded in AMRs that enables them to detect and avoid obstacles in real time. Using sensors and advanced algorithms, AMRs can safely navigate through crowded and dynamic environments like busy warehouses, where the constant movement of goods and workers occurs. This technology ensures that AMRs maintain their efficiency and speed without causing collisions or delays while operating autonomously.
LiDAR (Light Detection and Ranging)
A key technology AMRs use to accurately measure distances is the emission of laser light and the analysis of reflection. This allows the AMR to create precise, high-resolution maps of its surroundings, essential for navigation and obstacle detection. By leveraging LiDAR, AMRs can navigate complex environments, avoid obstacles, and dynamically adjust their paths, ensuring smooth and efficient movement across a warehouse.
Simultaneous Localization and Mapping (SLAM)
Simultaneous Localization and Mapping (SLAM) is a cutting-edge technology used by Autonomous Mobile Robots (AMRs) to build a map of their surroundings while simultaneously tracking their own location in real-time. Using sensors like LiDAR and cameras, SLAM enables AMRs to dynamically understand and navigate their environment without relying on pre-set paths. This allows them to detect and avoid obstacles, adjust routes on the fly, and operate efficiently even in changing warehouse layouts. The use of SLAM technology dramatically enhances the accuracy and efficiency of AMRs, enabling them to work seamlessly in dynamic and complex environments with minimal human oversight.
Payload Capacity
This is the maximum weight an AMR can safely transport without compromising its performance. Different AMRs are designed to handle varying payloads, catering to specific warehouse needs. Some may be optimized for lighter loads and faster movement, while others are engineered to transport heavy materials over long distances. Selecting the right AMR with the appropriate payload capacity ensures that operations are both efficient and cost-effective, reducing the need for manual handling or additional equipment.
Common Types of Software Used in Warehouses
Warehouse Management System (WMS)
A Warehouse Management System (WMS) is integral to supply chain operations and provides a comprehensive software solution designed to manage key operations within a warehouse. This includes tasks such as inventory control, slotting,cubic optimization, order processing, and shipment tracking. Warehouse Management Software also allows for various types of common warehouse processes such as batch picking and wave picking. For instance, a WMS can direct AMRs to pick items, restock shelves, or transport goods efficiently, ensuring seamless operations throughout the warehouse. This integration not only boosts productivity but also minimizes errors and speeds up order fulfillment, making WMS a critical component in modern warehouse automation.
WMS packages are offered with a broad spectrum of features and capabilities, varying from basic inventory management to more advanced functions, such as Warehouse Control Software (WCS) and Warehouse Execution Systems (WES). These additional components play a vital role in managing both manual and automated systems, ensuring that all aspects of warehouse operations are aligned.
A WMS often communicates with other essential software components like Enterprise Resource Planning (ERP) systems as well as specific components such as Fleet Management System (FMS) to streamline operations further. This interconnectedness ensures that all warehouse functions, from inventory to fulfillment, are managed efficiently, enabling businesses to maximize their automation potential.
Warehouse Control Software (WCS)
Warehouse Control Software (WCS), can be found as a part of a WMS or as a standalone software. WCS works in tandem with a WMS by taking instructions from the system and communicating with various machine controllers across a semi-automated or fully automated warehouse. While the WMS determines what needs to happen (e.g., moving a package from storage to shipping), the WCS ensures that these instructions are executed by coordinating machine movements.
For example, when a package needs to be sent from storage to shipping, the WCS communicates with barcode scanners, conveyors, and sorters, ensuring the package is tracked and directed appropriately. It handles the timing and communication between machine controllers, such as Programmable Logic Controllers (PLCs), label printers, and scanners.
WCS is commonly used in fixed asset automation, such as conveyors and sorting systems. While it can interface with AMR-related software, such as Fleet Management Systems, most WCS packages do not optimize the movement of AMRs directly.
Fleet Management System (FMS) or Warehouse Execution System (WES)
Fleet Management System (FMS), sometimes called Warehouse Execution System (WES), is a specialized software platform that coordinates and controls a fleet of AMRs within a warehouse or facility. FMS optimizes task distribution by assigning the right robot to the right job, ensuring that routes are efficient and that AMRs don’t collide or interfere with one another. It monitors the status of each robot in real time, manages maintenance needs, and adjusts workloads based on current operational demands. By centralizing control over multiple robots, FMS boosts overall productivity, reduces downtime, and ensures smooth, efficient operations across the entire fleet.
Enterprise Resource Planning (ERP)
ERP is a type of business management software that helps companies manage their day-to-day operations. ERP systems integrate and centralize data and resources across multiple departments, including finance, HR, manufacturing, supply chain, and more.
Terms in Warehouse Operations Procedures
ABC Classification
A method of inventory classification that groups items based on their value and usage. A-items are the most valuable and have the highest usage; B-items are less valuable and have lower usage; and C-items are the least valuable and have the lowest usage. ABC classification optimizes inventory management and ensures that the most important items are always in stock.
Slotting
The process of assigning items to specific locations in the warehouse. Slotting optimizes picking and put-away efficiency.
Discrete Picking
Discrete picking is a method used in warehouse operations where a worker picks items for one order at a time. In this process, the picker receives a single order, retrieves all the required items from their storage locations, and completes the order before moving on to the next one.
This approach is simple and straightforward, as it involves handling one order from start to finish, which minimizes the risk of errors or confusion. Discrete picking is particularly effective for small to medium-sized orders or in warehouses with lower order volumes. However, it is less efficient in high-volume operations, where batch or wave picking methods are often preferred to optimize time and resources.
Batch Picking
Batch picking in warehouse operations is a method of order fulfillment where a worker (or an Autonomous Mobile Robot, in some cases) picks items for multiple orders simultaneously rather than one order at a time. Instead of completing one order before starting the next, the worker collects all the items needed for several orders in a single trip through the warehouse.
This process improves efficiency by reducing the number of trips required to retrieve items and optimizing travel time. After batch picking, the items are typically sorted into individual orders at a packing station or through automated sorting systems. Batch picking is especially beneficial in high-volume environments with many small, similar orders.
Wave Picking
Wave picking is a method used in warehouse operations where orders are grouped and picked in waves, based on specific criteria such as order priority, shipping schedules, or product types. Unlike batch picking, where multiple orders are picked simultaneously, wave picking involves organizing orders into sets or “waves,” which are then picked in a designated time frame.
This method allows for better coordination between different warehouse activities, such as picking, packing, and shipping. By aligning picking operations with shipping schedules, wave picking helps ensure that products are ready for dispatch at the right time, improving overall efficiency and reducing bottlenecks. It is particularly useful in large-scale warehouses with complex logistics.
Zone Picking
Zone picking is a method used in warehouse operations where the storage area is divided into different zones, and workers are assigned to pick items only from their designated zone. When an order requires products from multiple zones, each worker picks the items from their specific zone, and the order is either consolidated later or passed from one zone to another for further picking.
This method increases efficiency by reducing travel time, as workers focus on smaller, designated areas rather than moving throughout the entire warehouse. Zone picking is especially effective in large warehouses with high order volumes, as it allows for faster and more organized fulfillment. Additionally, it can be combined with other picking methods, such as batch or wave picking, to further streamline operations and improve order accuracy.
Order Line
In warehouse operations, an order line refers to a single item or SKU (Stock Keeping Unit) on a customer order, but it can represent varying quantities and units. For instance, a line might include a single SKU or multiple units of the same SKU, and those units can be packaged differently, such as in cases, pallets, or individual items. The flexibility of a line allows warehouses to manage different types of orders efficiently, whether the customer is ordering a single product or bulk quantities. Understanding this helps streamline picking and packing processes for more accurate and efficient fulfillment.
Lines Per Hour
Lines per hour in warehouse operations is a performance metric that measures the number of order lines a worker or system can pick, pack, or process within one hour. An order line refers to a distinct item or SKU (Stock Keeping Unit) listed on a customer’s order. For example, if an order contains three different products, it would consist of three lines.
This metric is used to gauge the productivity of warehouse staff or automated systems and is critical for evaluating the efficiency of order fulfillment processes. A higher lines per hour rate indicates a faster and more efficient operation, which is key to meeting demand in high-volume warehouses. It also helps in identifying areas for improvement in workflows, staffing, and automation.
Units Per Hour
Units per hour is a key performance metric in warehouse operations that measures the number of individual items (or units) processed, picked, packed, or shipped in one hour. This metric provides insight into the efficiency and productivity of the workforce or automated systems within the warehouse.
Tracking units per hour helps managers evaluate how quickly orders are being fulfilled, optimize workflows, and identify areas for improvement. Higher units per hour reflect a more efficient operation, which is crucial for meeting customer demand and maintaining smooth operations in a high-volume warehouse environment.
Picks Per Hour
Picks per hour is a common performance metric in warehouse operations that measures the number of individual picking actions a worker or automated system completes within one hour. A “pick” refers to the act of retrieving a specific item or SKU from its storage location to fulfill an order.
This metric is essential for evaluating the efficiency of the picking process, as it helps track how quickly orders are being gathered. A higher pick per hour rate indicates a more efficient operation, while a lower rate may signal opportunities for improvement in workflow design, worker training, or automation. Monitoring this metric allows warehouses to optimize labor, reduce operational costs, and improve order fulfillment speed.
Pick Module
A pick module is a specialized area within a warehouse designed to streamline the order picking process by organizing products for efficient retrieval. It is typically a multi-level structure that consolidates various storage types, such as pallet racks, carton flow racks, and shelving, into a single area to optimize space and picking speed.
In a pick module, products are arranged in a way that minimizes travel time for workers or automated systems, allowing them to pick items faster and more efficiently. These areas are often equipped with conveyors (powered or gravity), gravity-fed racks, or other systems to move items quickly through the picking process.
Putting These Terms to Use
Understanding the terminology surrounding Autonomous Mobile Robots (AMRs) is essential for maximizing their potential in your warehouse operations. By familiarizing yourself with these key concepts, you can make informed decisions about implementing AMRs effectively, ensuring your facility runs smoothly and efficiently. As AMR technology continues to evolve, staying up-to-date with these advancements will allow you to enhance productivity, reduce operational costs, and maintain a competitive edge in the ever-changing world of logistics. Whether you’re looking to streamline material handling or optimize order fulfillment, adopting AMRs is a smart move toward future-proofing your warehouse.