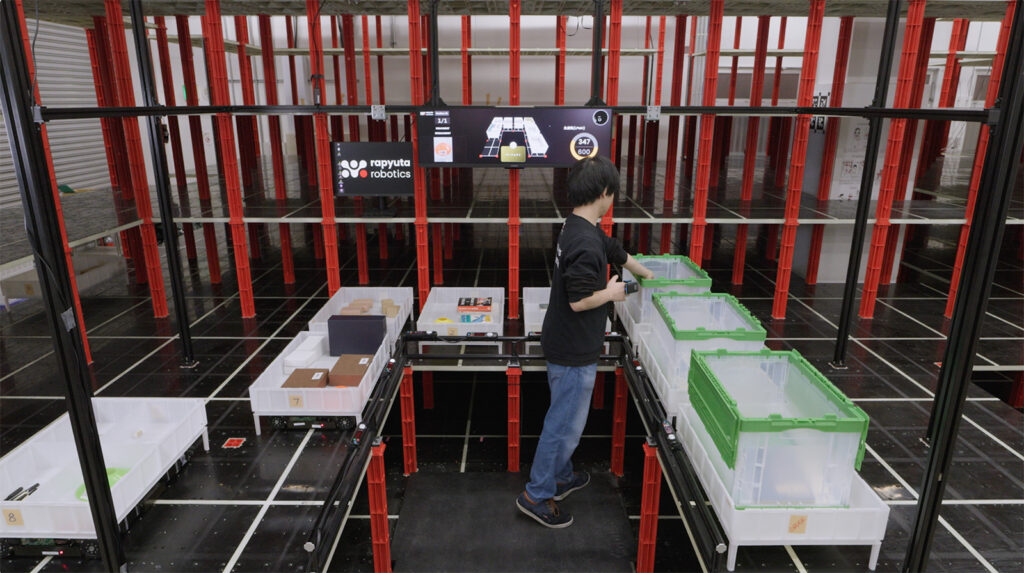
Introduction: The Need for Smarter Warehouse Automation
Warehouses and distribution centers (DCs) are under constant pressure to increase efficiency, reduce costs, and keep up with growing demand. The rise of e-commerce, labor shortages, and space constraints have forced logistics and operations leaders to rethink traditional warehouse processes.
One technology that is rapidly transforming fulfillment operations is Automated Storage and Retrieval Systems (ASRS). These systems streamline picking, improve space utilization, and reduce dependency on manual labor—all critical factors in meeting today’s operational challenges.
According to the STIQ 2024 G2P Solutions Report, warehouse automation, including ASRS, is seeing accelerated adoption, with penetration levels reaching 20% of total addressable market (TAM). While this marks significant growth, it also highlights vast untapped opportunities for businesses looking to gain a competitive edge.
For warehouse managers, directors of engineering, and decision-makers looking to scale operations, the question is no longer if automation is necessary, but which solution will deliver the best return on investment (ROI)?
This article explores why ASRS is becoming essential for modern distribution centers and how Rapyuta ASRS solution provides a flexible, scalable, and cost-effective path to automation.
Challenges in Traditional Warehouse Operations
1. Picking Inefficiencies Reduce Throughput
In conventional warehouses, workers spend more time walking between storage locations than picking items. A typical cart-picking process takes 72 seconds per pick, with 56 seconds spent walking and only 16 seconds on picking. This inefficiency limits overall throughput, making it difficult to meet high-order demand without increasing headcount.
ASRS eliminates unnecessary walking by delivering items directly to pickers, increasing productivity and reducing fulfillment times.
2. Poor Space Utilization Increases Costs
Many warehouses operate at less than 30% vertical storage efficiency because of traditional racking systems. Fixed shelving and wide aisles waste valuable space, leading to:
- Higher operational costs per pallet stored
- Increased real estate expenses
- Limited ability to scale operations without major infrastructure investments
By using vertical storage and automated retrieval, ASRS optimizes space usage and enables higher storage density within the same warehouse footprint.
3. Labor Challenges Drive Up Costs
Warehousing and logistics face a growing labor shortage, with demand for warehouse workers increasing 15% year-over-year. Hiring, training, and retaining staff for repetitive picking tasks is both costly and unsustainable.
By reducing reliance on manual labor, ASRS enables warehouses to:
- Lower overall labor costs
- Improve worker safety by reducing strain from repetitive tasks
- Adapt to seasonal demand spikes without hiring surges
4. Manual Picking Errors Impact Order Accuracy
Human-driven picking leads to errors in 3-5% of orders, resulting in:
- Increased return and reprocessing costs
- Customer dissatisfaction due to incorrect shipments
- Inefficiencies in inventory management
ASRS improves accuracy through automated retrieval, guided picking, and real-time validation, significantly reducing picking errors to near-zero levels.
How Rapyuta ASRS Transforms Warehouse Operations
Rapyuta ASRS provides a scalable and efficient solution to these challenges by automating storage, retrieval, and order fulfillment. With faster picking, higher accuracy, and better space utilization, warehouses can process more orders with fewer resources.
1. Higher Productivity and Faster Order Fulfillment
By removing unnecessary walking and manual searching, Rapyuta ASRS enables a 10X increase in picking speed. Each picking station can present 400 bins per hour, ensuring operators are never waiting for inventory.
The result? Faster fulfillment, higher throughput, and reduced labor costs.
2. Optimized Storage Efficiency
Rapyuta ASRS increases storage density by 2.5X compared to traditional racking. The system:
- Utilizes vertical storage to maximize warehouse space
- Reduces aisle widths, allowing more inventory per square foot
- Adapts to different warehouse layouts, enabling flexible configurations
This means warehouses can store more inventory without expanding their footprint.
3. Reduced Operational Costs and Increased ROI
With fewer labor requirements, higher accuracy, and improved efficiency, Rapyuta ASRS reduces:
- Direct labor costs by up to 30%
- Order errors, lowering return and rework expenses
- Energy consumption through intelligent power management
Warehouses that implement ASRS recover their investment within 2-4 years through higher productivity and lower operating expenses.
Why Forward-Thinking Warehouses Should Invest in Rapyuta ASRS
While many ASRS solutions exist, Rapyuta ASRS stands out with:
1. Advanced Robotics for Maximum Efficiency
- Ultra-thin (3-inch) robots that operate seamlessly under storage units
- Mecanum wheels for 360-degree movement, optimizing retrieval paths
- RFID navigation and AI-powered optimization, ensuring precision
2. Modular and Scalable Storage Design
- Multi-floor ASRS with intelligent elevator systems for seamless vertical transport
- Flexible bin configurations, supporting multi-SKU storage
- Expandable system that grows with your business needs
3. Seamless Deployment Without Disrupting Operations
- Rapid assembly with modular construction, no need for costly infrastructure changes
- Allows gradual migration from existing racking to ASRS without downtime
- Easily integrates with existing Warehouse Management Systems (WMS)
Understanding the Business Impact: A Data-Driven Comparison
Metric | Traditional Warehouses | Rapyuta ASRS-Enabled Warehouses |
Picking Throughput | 50 UPH | 400 UPH (8X higher) |
Storage Utilization | <30% of warehouse space | 2.5X more efficient |
Order Accuracy | 95-97% | 99.9% accuracy |
Labor Costs | High | 30% cost reduction |
Scalability | Limited | Easily expandable |
These numbers demonstrate that ASRS is not just an operational improvement—it’s a competitive advantage.
Conclusion: Next Steps Toward Warehouse Automation
The warehousing industry is evolving, and automation is no longer an option—it’s a necessity. With increasing demand, labor shortages, and the need for greater efficiency, ASRS provides a clear path to scalable and cost-effective operations.
For decision-makers evaluating automation, the next steps are:
- Assess your warehouse’s current pain points—Where do inefficiencies exist?
- Quantify the benefits of ASRS for your operation—What savings and productivity gains are possible?
- Explore a tailored ASRS implementation plan—How can you integrate automation seamlessly?
Want a data-backed ASRS strategy for your warehouse? Let’s discuss how Rapyuta Robotics can help.