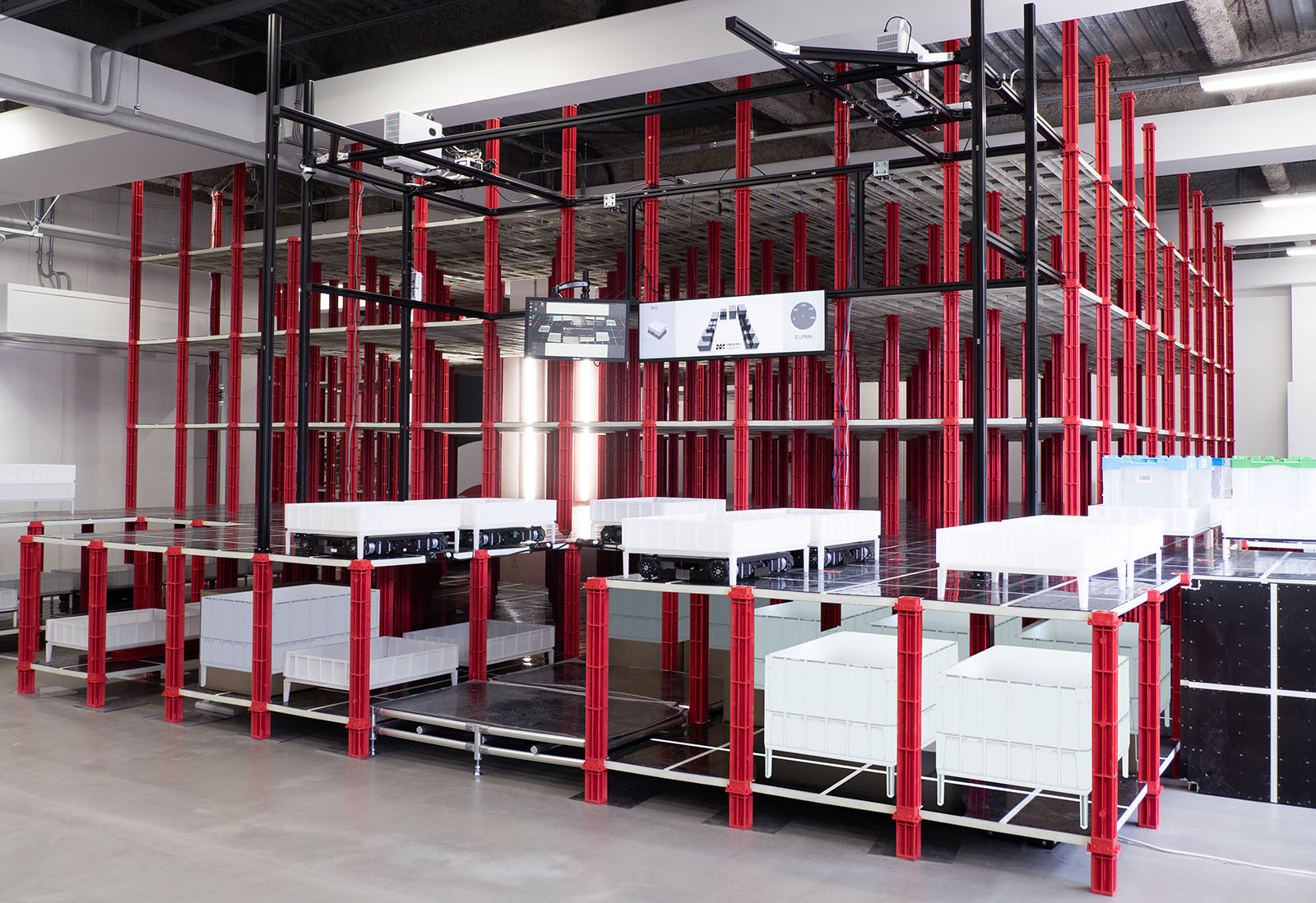
What is an Automated Storage and Retrieval System (ASRS) in a warehouse?
An Automated Storage and Retrieval System (ASRS) is a technology-driven solution that automates the placement and retrieval of inventory within a warehouse. It maximizes storage space, increases picking speed, and reduces labor dependency by using robotic systems, conveyors, and integrated software to handle goods efficiently.
Warehouses in the United States are facing growing challenges—space constraints, labor shortages, and rising operational costs. As customer expectations for faster deliveries increase, traditional storage and retrieval methods are struggling to keep up.
This is where Automated Storage and Retrieval Systems (ASRS) come into play. These systems are transforming how warehouses operate by maximizing storage space, reducing errors, and improving efficiency. ASRS isn’t just about automation; it’s about creating a warehouse that’s ready to handle today’s demands while preparing for future growth.
In this blog, we break down the top seven reasons why ASRS is becoming an essential part of warehouse operations and how its helping businesses stay competitive in a challenging environment.
1. Optimizing Space Utilization
Space is one of the most valuable assets in warehousing, and ASRS ensures every inch is utilized effectively. By enabling vertical storage, businesses can increase capacity by up to 85% without needing to expand their physical footprint. This is especially beneficial for urban warehouses, where space is at a premium.
Whether dealing with warehouses featuring columns, beams, or mezzanines, ASRS systems adapt to complex layouts, making them versatile for different environments.
2. Enhancing Operational Efficiency
Traditional storage systems often involve long travel times for workers retrieving items from shelves. ASRS eliminates this inefficiency by automating these tasks, drastically reducing retrieval times and speeding up order processing.
A typical ASRS system can handle up to 400 retrievals per hour, ensuring orders are fulfilled faster, especially during peak seasons. This improvement enables warehouses to meet the growing demands of same-day or next-day delivery services.
3. Reducing Labor Dependency
The U.S. warehousing industry has faced chronic labor shortages in recent years, with turnover rates reaching nearly 50% annually. ASRS addresses this challenge by automating repetitive and labor-intensive tasks, reducing the dependency on human labor.
Instead of hiring and training seasonal workers, warehouses can allocate their existing workforce to higher-value tasks such as quality control and customer service, improving overall productivity.
4. Minimizing Errors in Order Fulfillment
Errors in order picking can lead to costly returns, dissatisfied customers, and operational inefficiencies. ASRS minimizes these errors by integrating advanced tracking systems that ensure accurate picking and retrieval.
With error rates dropping to as low as 0.1%, ASRS significantly reduces order discrepancies and builds customer trust through reliable and accurate deliveries.
5. Supporting Scalability Without Disruptions
The ability to scale operations quickly is critical for warehouses, especially during peak seasons or periods of business growth. ASRS systems are designed to grow alongside your business without requiring downtime.
Whether you’re adding more bins or expanding storage capacity, ASRS enables seamless scaling, ensuring operations continue uninterrupted—a feature that’s invaluable for meeting fluctuating demands.
Worried About Efficiency, Integration, or ROI?
6. Improving Inventory Management
ASRS integrates with Warehouse Management Systems (WMS) to provide real-time visibility into inventory levels. This integration not only ensures accurate stock tracking but also minimizes overstocking and understocking issues.
With better inventory control, warehouses can optimize their stock levels, reduce waste, and ensure products are always available when needed—all while cutting storage costs by up to 20%.
7. Enhancing Workplace Safety
Safety is a top priority in warehouses, and ASRS plays a significant role in creating safer environments. By automating high-bay storage and reducing the reliance on forklifts, ASRS significantly lowers the risk of workplace accidents.
Additionally, the system’s precision eliminates the need for workers to climb ladders or handle heavy loads, creating a safer and more ergonomic workspace.
What makes Rapyuta ASRS different from traditional automated storage systems?
Rapyuta ASRS stands out due to its anchorless, modular, and relocatable design, allowing it to fit challenging warehouse layouts—such as those with beams, mezzanines, or rental spaces—without disrupting operations. Unlike most systems, it’s easily scalable and can be moved to new facilities as your business grows, making it the most adaptable ASRS on the market.
Why Rapyuta ASRS is the Ideal Choice
Rapyuta ASRS stands apart in its ability to adapt, scale, and ensure accuracy. Designed to meet the diverse needs of modern warehouses, Rapyuta ASRS is not only a cutting-edge solution but also one tailored for operational challenges across various warehouse configurations.
1. Flexibility and Scalability: Versatility for Your Business Expansion
Flexible Layouts for Any Warehouse
Rapyuta ASRS is designed to adapt to any warehouse shape, including spaces with challenging layouts like columns, beams, or upper floors where anchor installations are not feasible. Whether you’re working in a rental warehouse, installing on the first floor or mezzanine, or expanding operations, our system ensures the best use of available space.
Seamless Scalability
Unlike other ASRS solutions that require halting operations during expansions, Rapyuta ASRS allows your warehouse to scale without interrupting workflows. This makes it an ideal solution for businesses planning to grow or integrate automation into operational facilities.
Relocatable for Changing Needs
With its anchorless structure and modular design, the Rapyuta ASRS is the only relocatable ASRS on the market, allowing for flexible layouts and seamless scalability as your business grows. In an unpredictable business environment, it can be transferred to new locations with minimal cost and effort, ensuring long-term adaptability and sustained value.
Storage Efficiency: Maximizing Space Utilization Beyond Vertical Expansion
Fit Any Shape
Rapyuta ASRS can be assembled like building blocks, making it ideal for existing warehouses with complex layouts. By accommodating columns, beams, and mezzanines, it ensures no corner of your warehouse goes unused.
Minimizing Aisle Space
Most ASRS systems require wide aisles for robot movement, but Rapyuta’s innovative fleet control technology enables bins to be densely packed in multiple rows. When a target bin is needed, our robots work collaboratively to temporarily remove and replace front bins, significantly improving storage efficiency.
Customizable Bin Heights
With options for standard 24.8-inch (63 cm) poles and shorter 20.8-inch (53 cm) poles, Rapyuta ASRS offers the flexibility to optimize storage for items like small parts or stationery. This customization maximizes your storage capacity based on your inventory requirements.
3. Error Elimination: Triple Error Prevention for Seamless Operations
Display Navigation
A visual guide at the picking station ensures workers can intuitively and accurately perform tasks. With clear instructions on item location, quantity, and bin movement, this system eliminates language barriers and reduces errors.
Motion Capture Monitoring
Equipped with dual motion capture cameras, the system alerts workers with a sound and red light if they attempt to pick from the wrong bin or scan the incorrect item. This real-time feedback ensures every action is precise.
Finish Button Validation
After each task, workers must press the Finish Button to confirm completion. If any error is detected, the button will remain unresponsive, prompting corrective action. This triple-layer error prevention system ensures flawless execution, even for new employees.
Conclusion: A Future-Ready Solution
Rapyuta ASRS offers unparalleled flexibility, space optimization, and accuracy, making it the ultimate choice for warehouses seeking a competitive edge. Its ability to adapt to any layout, scale seamlessly, and ensure error-free operations sets it apart as the most advanced ASRS solution in the market.
Is your facility ready to tackle storage challenges and optimize its operations for the future? Let’s talk how Rapyuta ASRS can take your warehouse to the next level.
FAQs
- Can Rapyuta ASRS be installed in warehouses with complex layouts?
Yes, Rapyuta ASRS is specifically built for layout flexibility. Whether your warehouse has columns, multi-floor levels, or unusual dimensions, the system can be assembled like building blocks to fit irregular shapes and make the best use of available space—without requiring major structural changes or anchors.
- How does Rapyuta ASRS improve storage efficiency?
Rapyuta ASRS uses a multi-row bin packing system with innovative fleet control, minimizing the need for wide aisles. Its robots can temporarily remove front bins to access rear ones, allowing bins to be packed tightly. Plus, customizable bin heights ensure you maximize space for various item sizes—from stationery to small parts.
- How does Rapyuta ASRS prevent errors during order picking?
Rapyuta ASRS features a triple-layer error prevention system: visual guides at picking stations, dual motion capture cameras for real-time monitoring, and a Finish Button that only activates after task validation. These layers ensure high accuracy even for new or multilingual workers, minimizing errors to near zero.
- Is Rapyuta ASRS scalable and future-ready for business growth?
Absolutely. Rapyuta ASRS is designed for seamless scalability—you can expand your system without stopping operations. Its modular and relocatable design also means you can scale up or move locations as needed, offering long-term flexibility and cost-effectiveness for growing businesses.