Introduction
In the modern supply chain, warehouse efficiency is no longer a luxury—it’s a necessity. As customer expectations for faster delivery times and accurate order fulfillment grow, traditional manual warehousing methods are struggling to keep pace. The limitations of human labor, physical storage constraints, and inconsistent performance are creating bottlenecks that restrict growth and profitability.
Rapyuta Automated Storage and Retrieval System (ASRS) offers a powerful solution by increasing storage efficiency by 2.5X and boosting picking productivity by up to 10X. Through advanced automation, real-time tracking, and modular design, Rapyuta ASRS eliminates the inefficiencies of manual warehousing while delivering unmatched flexibility and performance.
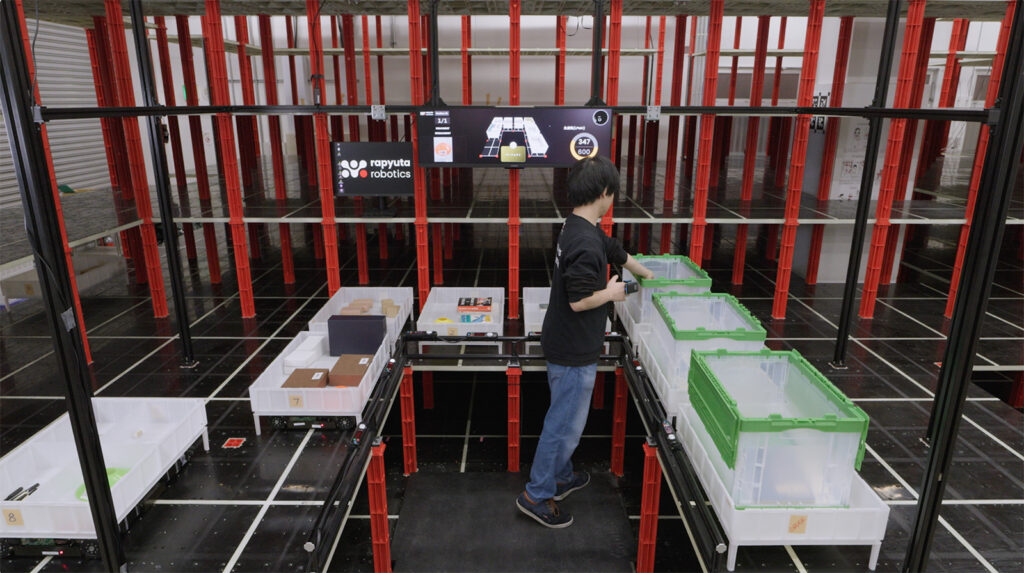
This guide provides a detailed comparison of Rapyuta ASRS versus manual warehousing, focusing on how automation enhances storage utilization, picking efficiency, accuracy, scalability, and cost control.
1. Maximize Storage Efficiency by 2.5X
Storage capacity is a critical factor in warehouse profitability, yet most warehouses fail to use available space effectively. Manual warehousing systems are limited by human access requirements, which restrict storage density and prevent full use of vertical space.
In manual warehousing, the need for wide aisles to accommodate human access, forklifts, and other material-handling equipment reduces the overall storage footprint. Furthermore, vertical space is underutilized because manual systems are limited to the height that operators can comfortably reach. Expanding storage in a manual environment often requires costly structural modifications, such as adding mezzanine levels or expanding the warehouse footprint.
Limitations of Manual Warehousing:
Manual Warehousing Challenges | Impact on Operations |
Underutilized vertical space | Less than 30% of vertical warehouse space is used |
Wide aisle requirements | Reduces storage density and available inventory space |
Fixed rack configurations | Limits flexibility and reconfiguration options |
Difficulty scaling capacity | Expanding storage requires structural modifications |
How Rapyuta ASRS Improves Storage Efficiency:
Rapyuta ASRS is designed to maximize the use of vertical and horizontal space through a modular block-based architecture. The system is built with a ground floor, poles, and plates that can be adjusted based on warehouse height and layout requirements.
Manual Warehousing | Rapyuta ASRS |
Less than 30% of vertical space is utilized | Two pole height options enable flexible configurations of up to 7 or 9 storage levels—not limitations, but customizable design choices. |
Wide aisles required for human access | Narrow aisles as robots navigate independently |
Fixed rack configurations limit flexibility | Modular block-based design allows custom layouts |
Difficult to expand without facility changes | Simple expansion by adding more modules and robots |
- High-Density Vertical Storage:
- Rapyuta ASRS provides two pole height options to accommodate different inventory sizes. Depending on the chosen structure height, storage can be configured with up to 7 or 9 levels—not as a limit, but as flexible design options to suit the needs
- Each BIN can hold up to 30 kg (66 lbs.) of product weight, supporting a total load capacity of 1,576 lbs. (715 kg) per square meter.
- Automated bin stacking and retrieval enable higher density storage without increasing labor requirements.
- Compact Aisle Design:
- Manual systems require wide aisles for human access and equipment operation.
- Rapyuta ASRS robots operate on narrow tracks, reducing aisle width and increasing available storage capacity.
- The robots’ ability to move in four directions without needing to turn allows for maximum use of floor space.
- Flexible and Scalable Configuration:
- Rapyuta ASRS is built using a modular design, which allows for quick expansion without structural changes.
- The system can be reconfigured to adapt to changing inventory profiles or order volumes.
Results:
- 2.5X increase in total storage capacity.
- Up to 40% reduction in aisle width, freeing up more storage space.
- Increased storage density without expanding the facility size.
How much space can ASRS save in your warehouse? Let’s calculate. Talk to us.
2. Boost Productivity by 10X
Order fulfillment speed is critical for customer satisfaction and operational efficiency. In manual systems, a large portion of the order cycle time is consumed by walking and searching for items. Operator fatigue and variability further limit overall performance.
Manual picking processes are slow because operators must manually locate, retrieve, and handle items. Inconsistent performance due to human fatigue and variability further reduces productivity. Operators spend up to 70% of their time walking between picks rather than picking items. Even the most efficient manual systems are limited by human speed and endurance.
Limitations of Manual Warehousing:
Manual Warehousing Challenges | Impact on Operations |
Excessive walking time | Up to 70% of working time is spent walking between picks |
Low picking rates | Average picking rate of 50 units/hour |
Inconsistent performance | Operator fatigue reduces productivity over time |
Idle time between picks | Time wasted while searching for the next item |
How Rapyuta ASRS Improves Productivity:
Rapyuta ASRS dramatically increases productivity by automating the retrieval and presentation of storage bins. Robots transport bins directly to the picking station, eliminating the need for walking and searching.
Manual Warehousing | Rapyuta ASRS |
Average picking rate of 50 units/hour | Up to 600 lines/hour per station |
Walking time reduces overall throughput | Direct bin delivery eliminates walking time |
High variability due to human limitations | Robots maintain consistent picking speed |
Idle time between picks | Continuous bin presentation eliminates downtime |
- Direct Bin Delivery:
- Rapyuta ASRS robots transport bins at a maximum speed of 6.27 mph (2.8 m/sec).
- This eliminates the need for human walking and searching.
- Multi-Bin Presentation:
- Each picking station can present up to 8 bins simultaneously.
- This allows the operator to pick continuously without waiting.
- Continuous Operation:
- While the operator picks from one bin, the next bin is already being prepared for delivery.
- This ensures no idle time between picks and maximizes throughput.
- Consistent Performance:
- Unlike human operators, robots maintain consistent speed and accuracy without fatigue.
- The system can handle up to 138 round trips per hour between the robot and the picking station.
Results:
- 10X increase in picking productivity.
- Up to 600 lines/hour per station.
- Consistent order fulfillment speed regardless of order complexity.
3. Improve Accuracy and Reduce Errors
Order fulfillment errors are one of the biggest contributors to increased operational costs and customer dissatisfaction. In manual warehousing, human error is a common challenge due to the reliance on manual item identification, counting, and picking. Even with experienced operators, mistakes like mis-picks, over-picking, under-picking, and incorrect order fulfillment are inevitable, especially during peak periods when workload pressure is high.
Manual picking processes often involve operators visually scanning racks to identify products, which increases the chances of selecting the wrong item—especially when products are similar in appearance or when storage locations are frequently changed. Inventory records in manual systems are prone to inaccuracies because they depend on manual input and tracking. Misplaced or mislabeled items can cause further errors, leading to order delays, returns, and customer dissatisfaction.
Challenges of Manual Warehousing:
Manual Warehousing Challenges | Impact on Operations |
High picking error rates | Up to 3% of orders contain mis-picks or errors |
Lack of real-time feedback | Errors often go unnoticed until after order shipment |
Misplaced or mislabeled items | Delays in order fulfillment and higher return rates |
Manual inventory tracking | Inventory discrepancies cause stockouts or overstocking |
Operator fatigue and distraction | Higher error rates during peak periods and long shifts |
How Rapyuta ASRS Improves Accuracy:
Rapyuta ASRS addresses these accuracy challenges through automation, real-time guidance, and intelligent error prevention systems. The system ensures that the right item is picked every time by providing the operator with clear, step-by-step instructions and real-time validation.
Manual Warehousing | Rapyuta ASRS |
High mis-pick rates due to human error | Automated guidance reduces mis-picks and improves accuracy |
No immediate feedback for incorrect picks | System alerts operator if wrong bin is accessed |
Manual tracking creates inventory gaps | Real-time inventory tracking ensures accurate stock levels |
High error rates during peak periods | Consistent accuracy even under high demand |
- Automated Guidance with LED Indicators:
- Rapyuta ASRS uses LED indicators to highlight the correct bin and guide the operator through the picking process.
- The operator receives both visual and audio feedback, reducing the likelihood of mis-picks.
- The system directs the operator’s hand to the correct item location, reducing reliance on manual searching.
- Real-Time Error Prevention:
- If the operator attempts to select the wrong bin or item, the system immediately issues a warning (audio and visual).
- The robot will not proceed to the next step until the correct item is selected, ensuring that the order is picked correctly the first time.
- The system records and monitors operator actions, enabling real-time identification and correction of errors.
- Inventory Tracking and Slotting:
- The ASRS system continuously updates inventory levels after each pick, maintaining real-time visibility into stock availability.
- Automated slotting ensures that high-turnover items are positioned for faster retrieval, further improving accuracy and speed.
- Operators are notified if an item is misplaced or missing, allowing for immediate correction.
- Reduction in Training Time:
- Unlike manual warehousing, where training new operators takes time, Rapyuta ASRS’s automated guidance allows new operators to start picking accurately with minimal training.
- The system’s guided picking process minimizes the need for operator experience, leading to consistent performance across shifts.
Results:
- Up to 99.9% picking accuracy due to real-time feedback and automated guidance.
- Reduced mis-picks and order errors result in fewer returns and higher customer satisfaction.
- Lower training time for new operators, leading to consistent performance across the workforce.
- Improved inventory accuracy reduces stockouts and overstocking, optimizing warehouse efficiency.
4. Scale Without Disruption
Scalability is one of the most significant challenges in manual warehousing. Expanding capacity in a manual warehouse typically involves increasing physical space, hiring additional labor, and reconfiguring storage layouts—often at considerable cost and operational disruption.
When order volumes increase, manual systems face significant bottlenecks because performance is tied to labor availability. Hiring more staff adds direct costs, and training new operators takes time, further delaying the ability to scale quickly. Performance also drops during peak seasons as human fatigue and error rates increase under pressure. Expanding storage capacity in a manual warehouse typically requires adding new rack systems and expanding floor space, which involves costly infrastructure changes.
Challenges of Manual Warehousing:
Manual Warehousing Challenges | Impact on Operations |
Increasing storage capacity requires structural changes | High costs and long lead times |
Performance drops during high order volume periods | Slower order fulfillment and higher labor costs |
Scaling requires hiring more labor | Increased costs and longer training cycles |
Lack of flexibility in storage configuration | Difficult to adjust based on demand fluctuations |
High turnover and seasonal labor challenges | Reduced consistency and performance during peak periods |
How Rapyuta ASRS Enables Fast and Flexible Scaling:
Manual Warehousing | Rapyuta ASRS |
Expanding capacity requires new infrastructure | Modular design allows fast expansion without downtime |
Performance drops under high order volume | Consistent high-speed performance under demand spikes |
Labor-dependent scalability | Robot-based system reduces reliance on labor availability |
Fixed storage layouts | Adjustable configurations to match product flow |
High turnover affects productivity | Automation ensures consistent performance |
- Preventive Maintenance Powered by AI & IoT
- Using a multifaceted approach, Rapyuta combines AI-based failure prediction, digitized usage data, and predictive maintenance time calculation to prevent downtime.
- The system continuously collects operating hours for each component, re-validates parts, and schedules timely replacements — all without halting warehouse operations.
- Modular Design for Seamless Expansion
- Add new robots or storage blocks in phases without downtime. The modularity supports both vertical and horizontal scaling, reducing dependency on infrastructure overhauls.
- Flexible Configuration
- Reconfigure storage layouts easily based on evolving product profiles and order patterns.
- Independent Robot Network
- Multiple robots operate simultaneously, managed by smart traffic control, ensuring uninterrupted, collision-free operations even during peak demand.
- Consistent Peak Performance
- With high-speed robots (up to 6.27 mph) and automation-driven workflows, the system consistently delivers up to 400 bins/hour per station, even during demand spikes.
- Minimal Labor Dependency
- Automation reduces the need for seasonal hiring, keeping labor costs low while maintaining stable output.
Results:
- Fast expansion without major capital investment or operational disruption.
- Consistent picking rates of up to 400 bins/hour per station, even under high demand.
- Increased flexibility to handle product mix changes and order volume spikes.
- Lower labor costs and reduced dependency on seasonal hiring.
Conclusion
Rapyuta ASRS transforms warehouse operations by increasing storage capacity by 2.5X and boosting picking productivity by 10X. Its modular design allows for quick scaling without major infrastructure changes, while automated systems improve accuracy and reduce operating costs. The system’s ability to maintain consistent performance during peak demand ensures that warehouses can handle higher order volumes without compromising quality or efficiency.
The shift from manual to automated warehousing is no longer optional—it’s a strategic necessity. Rapyuta ASRS provides a future-proof solution that enhances efficiency, accuracy, and scalability, positioning warehouses to meet the growing demands of modern supply chains.
To learn more about how Rapyuta ASRS can optimize your warehouse operations, contact us today for a consultation.