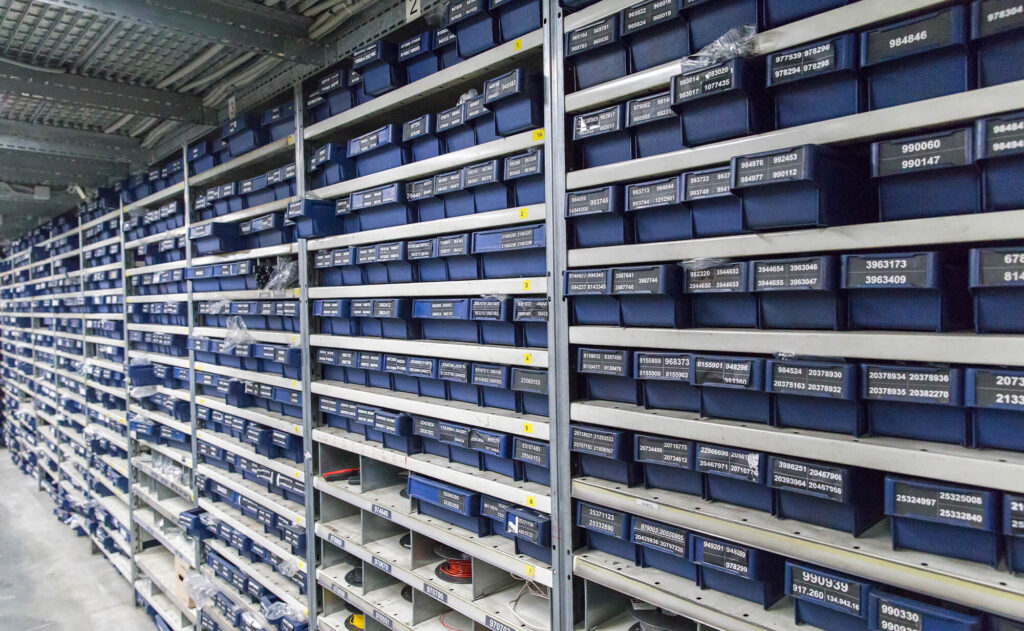
In the automotive industry, precision is paramount—not just on the assembly line, but in the supply chain. Imagine this: a customer orders a cabin air filter for a popular pickup truck model, but your warehouse mistakenly ships one meant for a different model year. Or a dealership requests a progressive spring for a compact sedan, but receives a tapered wire suspension spring instead. The consequences? Frustrated customers, costly returns, and potentially damaged relationships. For some automotive component distributors, performance clauses in contracts often include monetary penalties for errors.
For warehouse leaders such as Directors and Vice Presidents of Operations, managing high-volume automotive parts distribution, errors like these can feel unavoidable, but they’re not acceptable. So, how do you overcome this challenge?
The Real Cost of Picking Errors in Automotive Warehousing
Let’s break it down:
- Frequency: How many picking errors does your facility experience daily? Weekly? Monthly?
- Financial Impact: What does it cost to process a return or replace a wrongly shipped item? Include the added costs of expedited shipping, labor, and customer compensation. Are there potential contractual penalties?
- Reputation: For many automotive warehouses, whether shipping to OEMs, retailers, or direct-to-consumer, mistakes undermine trust, disrupt production timelines, and strain partnerships.
For operations directors and VPs managing multiple facilities and hundreds of employees, the cumulative impact of misshipments can escalate quickly. Even a 1-2% error rate can lead to thousands of errors annually, each one affecting your bottom line.
The automotive industry has a long history of driving logistics operations, leveraging methodologies such as just-in-time (JIT) and Kanban to streamline processes and ensure efficiency. These systems, combined with Six Sigma’s goal of reducing errors to just 3.4 mistakes per million opportunities, reflect the automotive sector’s relentless pursuit of precision and quality. By minimizing waste and optimizing workflows, these principles uphold the industry’s high standards and align perfectly with modern robotics solutions for error reduction.
Why Human-Driven Processes Fall Short
Automotive parts picking presents unique challenges:
- Visual Similarities: Many components look nearly identical, making manual differentiation prone to error.
- Complex SKU Management: The sheer variety of parts, often with minor differences, makes traditional systems inadequate.
- High Volume: Employees are under pressure to fulfill thousands of orders daily, leading to fatigue and mistakes.
Even with well-trained staff, human limitations make flawless picking nearly impossible at scale. That’s where automation comes in.
Enter Rapyuta Robotics: Revolutionizing Picking with Robotics
Rapyuta Pick-Assist robotics is a solution designed to significantly reduce picking errors while enhancing operational efficiency. Here’s how it works:
- Picker Guidance System : The Rapyuta Robotics Picker Guidance System optimizes each worker’s journey, directing them to the most efficient robot to minimize travel time and boost productivity. Leveraging advanced vision systems and AI, Rapyuta Pick-Assist Robots guide associates to the correct items, significantly reducing reliance on manual judgment. This technology not only helps seasoned associates achieve higher KPIs but also supports newcomers unfamiliar with the warehouse layout. Additionally, the system enhances workload management by dynamically assigning pickers to loading and unloading zones during periods of low activity.
Refer to the below image to get an overview of how PGS works
- Error Detection: Real-time validation ensures the picked item matches the order, flagging potential errors immediately, allowing for quick corrections well before the chance that the wrong items leave the facility.
- Scalability: Whether you’re running a single warehouse or a multi-site operation, Rapyuta Robotics integrates seamlessly with your existing systems. Tier 1 and similar suppliers often need to stock older parts for spares, a task that typically involves navigating dustier, less-frequented areas of the warehouse. Pick-Assist Robots bring the advantages of automation to these challenging environments, offering efficiency and precision where fixed automation solutions don’t align with the financial realities of most operations.
By reducing human error, these robots improve picking accuracy, ensuring that the right parts reach the right customers every time.
Real Results: Why Precision Matters in Automotive Parts Shipping
For automotive parts warehouses, shipping errors are not just inconvenient—they’re disruptive. A single mistake can delay repairs, halt manufacturing, or damage a customer’s confidence in your service. With Rapyuta Robotics, you can:
- Meet Contractual Obligations: Maintain service-level agreements (SLAs) with OEMs and other partners.
- Enhance Customer Satisfaction: Deliver accurate, on-time shipments that build trust.
- Reduce Costs: Minimize returns, rework, and labor-intensive error correction.
Conclusion: Precision You Can Rely On
Whether Tier 1 or aftermarket, the automotive industry leaves no room for error, and neither should your warehouse operations. Frequent picking mistakes are a pain point you don’t have to live with. With Rapyuta Pick-Assist robotics, you can transform your warehouse into a model of efficiency and accuracy.
It’s time to eliminate the costs and frustrations of mispicking.
Contact Rapyuta Robotics today to explore how our robotic solutions can help your warehouse achieve near-perfect picking precision.