The “Working at Rapyuta” series celebrates some of the best minds at Rapyuta Robotics. Through interviews with employees, we bring you the real story that you won’t find elsewhere.
Working at Rapyuta
Takahiro Harumoto – Field Engineering, Operation manager
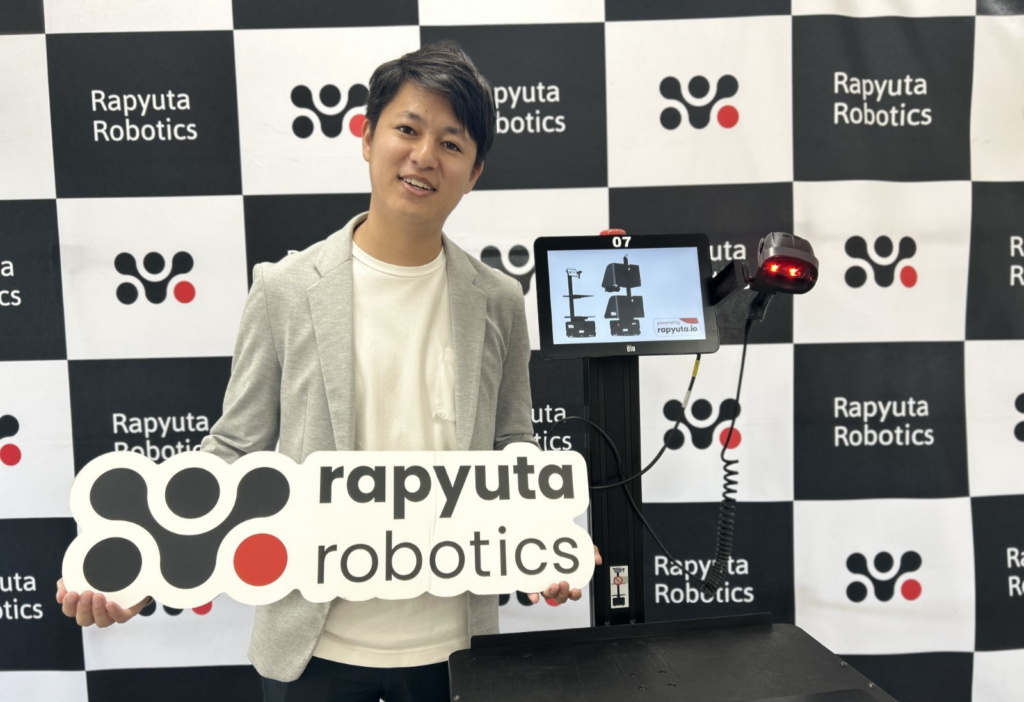
Joined the company in November 2021. After graduating from Kobe City University of Foreign Studies, I joined Nippon Express Co., Ltd. and was involved in productivity improvement and quality control of logistics processing, picking, and return operations at the customer’s logistics warehouse. After joining Rapyuta Robotics, he leveraged his on-site experience to work as a field engineer for the picking assist robot Rapyuta PA-AMR. He currently also serves as a team leader.
A career change from a non-IT industry—putting logistics site experience to use at Rapyuta
I majored in English at Kobe City University of Foreign Studies, and after graduation, I joined Nippon Express Co., Ltd., a major Japanese logistics company, as a new graduate, hoping to utilize my language skills and customs broker qualification that I obtained while in school.
I was assigned to a department in a customer’s logistics warehouse responsible for productivity improvement and quality control of logistics processing, picking, and return operations. I worked with a medical equipment manufacturer. Since the work involved facing and handling each issue together with the customer, it was honestly very demanding. However, when the results were reflected on-site and I received words of appreciation from the customer, I found it very rewarding.
During that time, I had the opportunity to work on the implementation of wearable devices, which sparked my interest in logistics tech. That led me to learn about Rapyuta Robotics. I was drawn to the company because I could directly apply my on-site logistics experience and also make use of my language skills, so I decided to change jobs.
When I first joined, I worked as a member of the field engineers for the Rapyuta PA-AMR (Picking Assist Robot). While the role was similar to my previous job and allowed me to leverage my experience, I struggled due to my lack of specialized knowledge, having come from a non-IT industry. I studied on my own, including obtaining certifications and actively engaged with internal departments to deepen my understanding through practical experience. Then, in January 2025, I was promoted to team leader and now also handle management duties in parallel.
The responsibility and joy of being a field engineer begins with sincerely listening to the customer’s voice
After the order and implementation of the Rapyuta PA-AMR are confirmed, the Project Management Team (PJM) creates the requirements definition, and based on that, each engineer proceeds with development. We field engineers mainly handle the phase right before and after the implementation.
Our specific tasks fall into five major categories: on-site testing, incident management, configuration changes, software updates, and robot withdrawal support.
The first task, on-site testing (to check for any gaps with the requirements definition), involves testing internally to confirm the development aligns with expectations, followed by verifying on-site at the actual warehouse to ensure there are no issues.
If the setup is complete according to the requirements, it goes smoothly, but that’s not always the case. Once, we even had trouble passing internal testing, and we received a lot of feedback from the customer. However, by clearly identifying the remaining issues and working through them one by one with internal departments, we were able to complete testing without losing the customer’s trust. During the real operation, we were able to demonstrate the full strength of our swarm control, and the customer even praised us for it.
After implementation, we handle tasks such as incident management, which I believe is the most important part of a field engineer’s duties. We are the first ones to visit the site and listen to the customers’ feedback directly. The most crucial thing is to first sincerely accept what the customer is saying. Without that, we can’t move forward or build trust.
So, I always listen openly to all feedback, clarify the issues, and share them with internal teams in an easy-to-understand manner. I believe this is the responsibility and role of a field engineer. While it can be very challenging, it’s also the most rewarding part. Being the first to receive praise makes me happy, and even when the feedback is harsh, turning it into a positive result brings me even more joy—and motivates me to keep going.
The core of a field engineer’s work: communication that connects the field and the internal teams
Smooth operations rely heavily on day-to-day communication. Especially at Rapyuta Robotics, where software updates occur very frequently, we need to constantly share the latest information and exchange opinions.
When visiting customer sites, I try to build relationships through small things like casually asking the workers, “How’s everything lately?” or greeting everyone I pass by.
Internally, I often work with the Project Management Team (PJM), engineers, and the Customer Success team (CS). With PJM, we mainly collaborate on test-related tasks. With CS, we coordinate the steps and key points for software updates and configuration changes. For more complex robot operations, I often communicate with engineers in India. Since communication with overseas engineers is in English, my English skills have improved significantly.
This way, the field engineer role requires collaboration with many departments and helps develop not only technical skills but also communication skills.
An environment where each person can fulfill their role by leveraging their strengths and experience
Currently, there are 7 field engineers (including myself) in the PA-AMR team. Our members range from young professionals to veterans, and we all work together, supporting each other to complete daily tasks.
I had no prior management experience in my previous job, so there’s still a lot I’m figuring out. But I try to create an open and positive work environment. Rather than micromanaging, I follow up as needed and encourage each person’s growth, aiming to maximize our team’s performance.
As for task assignments, we divide responsibilities based on positions and individual strengths. That said, since incident management is the most important duty of a field engineer, everyone is trained to handle it. However, we don’t need someone to be on call 24/7, and there are no overnight shifts. Some tasks like customer support and urgent maintenance at the site are outsourced, so our responsibilities are clearly divided. I feel this makes it easier to concentrate on our core tasks.
Furthermore, we have various career paths available, and people can aim for advancement based on their interests, strengths, and experience. The career paths include:
① Getting promoted within the same role to a management position
② Transferring to a different role
③ Becoming a field engineer for a different product.
I chose path ①. There have been past examples of ②, with people transferring to roles such as project manager or mechanical engineer. Path ③ also has precedents. In all cases, people are leveraging their previous experience and thriving in new fields.
Working at ever-evolving Rapyuta — enjoying the job while bringing out your full potential
What I find appealing about Rapyuta Robotics is the “products” and the “people.”
Regarding the products, with the continuous evolution of IT technology, large-scale upgrades and new features are added almost every year, allowing me to constantly engage with new technologies and systems. It’s truly exciting, and I sometimes wonder if there’s any other environment as captivating and fascinating as this.
When it comes to people, what I find interesting is diversity. It’s stimulating and enjoyable to work with people from various backgrounds, differing in language, culture, and career history. I can feel the attitude of trying to understand each other and get along, and I realize every day how glad I am to be working with this team.
In all of this, communication is crucial. This is also tied to the most important skill required of a field engineer. Since it’s necessary to negotiate directly with customers, internal stakeholders, and many others, good communication skills to build strong relationships are essential. This greatly contributes to smooth operations and teamwork.
Looking ahead as a team, our goal is to further strengthen the field engineer system. With the establishment of the India office and the growing number of engineers, we aim to continue enhancing collaboration between Japan and India and build a system that can support other products as well.
To achieve this, I would love to have someone join us who can take a broad view of the team, collaborate while working on tasks, and ideally help us systematize the operational structure of the team.
Since internal and external communication in business will primarily be conducted in Japanese, fluency in Japanese is a must. As for English, as long as you don’t feel uncomfortable with it, it’s not an issue. Although Rapyuta Robotics is a Japanese company, there are many opportunities to be exposed to a global environment, so those interested in English are more than welcome.
It’s a challenging position with a lot of responsibility, but it’s a highly rewarding job. If you’re someone who wants to work while enjoying your interactions with customers and colleagues, alongside the evolving Rapyuta Robotics, I encourage you to give it a try.
Rapyuta Robotics is looking for new team members!
[Visit the Careers Page Here]