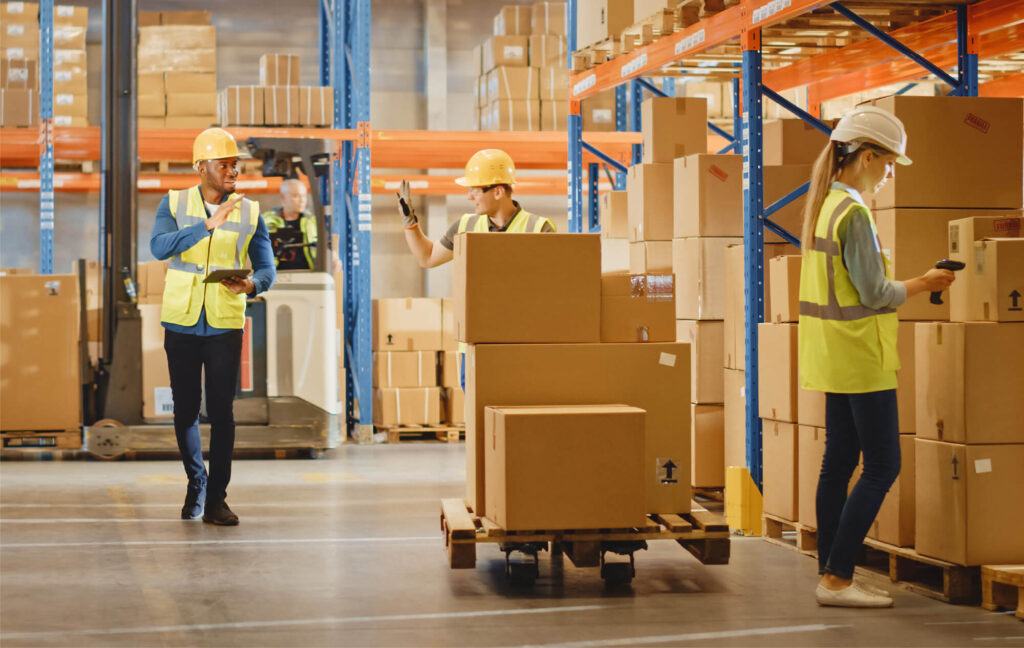
Hiring and retaining warehouse workers is a significant challenge, affecting companies both large and small. A recent article in The New York Times revealed that many of the 350,000 workers Amazon hired between July and October last year only stayed for a matter of weeks or even days. This high turnover rate highlights the struggles faced by employers trying to maintain a stable workforce in warehouse settings. Let’s explore some of the main obstacles to hiring and retaining warehouse workers today.
Low Pay
One of the most glaring issues is pay. Let’s face it: warehouse work is often not the highest-paying job in the entry-level market. When workers weigh their options, they may choose careers like plumbing, construction, or even flight attendants—positions that often offer higher wages and more growth potential. With so many alternatives available, it becomes harder to attract and retain warehouse employees.
Physically Demanding Work
Warehouse work is tough on the body. In roles such as pickers or stockers, employees can easily walk 6 to 10 miles per day on hard concrete floors, lifting heavy loads and making high-reach moves. This constant physical strain is exhausting and can deter workers from staying long-term. The nature of the job itself is a significant factor contributing to the high turnover rate.
This graph shows data from our customers in the 3PL and Retail industries, comparing walking times during picking activities with and without PA-AMRs. The black bars represent walking time with PA-AMR assistance, while the red bars show manual walking time. Above each pair, the percentage reduction highlights the time saved by implementing PA-AMRs, showcasing the efficiency gains achieved across various customer sites.
Challenging Work Environments
Many warehouses don’t maintain comfortable working temperatures. They can be extremely hot in the summer or, in the case of cold storage facilities, freezing cold all year round. These uncomfortable conditions add an extra layer of difficulty to an already physically demanding job. It’s no surprise that workers often leave for more comfortable environments.
Repetitive Tasks
Warehouse jobs tend to involve repetitive tasks that can quickly become monotonous. For example, picking 100 items per hour off shelves can make the work feel tedious and unfulfilling. While some employees might tolerate this for a short period, it’s not a long-term solution for most.
Lack of Flexibility
One major drawback in warehouse work is the lack of flexibility. Unlike other jobs that offer remote work or flexible schedules, warehouses operate on strict timelines. The last truck of the day has a set departure time, and the pressure is always on to get as much out the door as possible. This rigid structure can make it hard for employees to balance work and personal life, leading them to seek more flexible options elsewhere.
Limited Career Advancement
Warehouses typically have flat organizational structures with limited opportunities for career growth. For many employees, there’s no clear path for advancement, which can cause frustration and disillusionment. Without the prospect of moving up within the company, workers are often more likely to seek opportunities elsewhere.
Employee Burnout
The repetitive nature of the job, combined with the pressure to meet daily shipping targets, can lead to significant employee burnout. While managers are often incentivized to ensure that every package is processed and shipped on time, this pressure trickles down to the warehouse associates, who may struggle to keep up with the relentless pace. Over time, this leads to fatigue and eventual burnout.
Inadequate Training
Another significant challenge is the difficulty in providing adequate training to new hires. With such high turnover rates, it can be hard to ensure every new employee receives the comprehensive training they need. This can result in mispicks and mis-shipments, leading to operational inefficiencies. Proper training is critical, yet often neglected due to time constraints or resource limitations.
Seasonal Demand and Staffing Agencies
Many warehouses experience fluctuating demand, which requires flexible staffing levels. According to the career website Zippia, four of the top 10 warehouse employers in the US are actually staffing agencies. This reliance on temporary workers means companies often struggle with loyalty, as many of these employees are hired on a short-term, seasonal basis. Expecting commitment from seasonal workers can be unrealistic.
Recruitment Struggles
For small and mid-sized warehouse operations, recruitment presents its own set of challenges. Unlike large corporations like Amazon or Walmart, these businesses don’t have extensive resources to dedicate to recruitment efforts. In many cases, hiring is left to the warehouse manager, who may not have the expertise or time to thoroughly vet candidates. This can result in rushed decisions and hiring mistakes, exacerbating turnover issues.
A Brighter Path Forward
While the struggles are real, the future doesn’t have to look so bleak.
First, it’s important to remember that many people have found long-term, rewarding careers in logistics, supply chain, and warehouse work. From military veterans to employees of Fortune 50 companies, countless individuals have thrived in these roles. Even smaller companies, such as the local electronics distributor down the road, have success stories to tell.
Second, as leaders in logistics, we have the power to make meaningful changes in the industry. By leveraging technology,
One solution comes from Rapyuta Robotics, which offers Pick-Assist Autonomous Mobile Robots (PA-AMR) designed to reduce the physical strain on workers, improve training processes, and make work more enjoyable. Rapyuta’s core value of empathy drives their mission to automate the dirty, dull, and dangerous tasks, allowing human workers to focus on more intellectually stimulating and creative activities.
Their PA-AMRs are designed to assist in reducing the miles of walking required in a typical warehouse shift, alleviating some of the physical demands. These robots are equipped with intuitive touchscreens that help train new employees faster, getting them up to speed in a matter of hours instead of weeks. Additionally, the onboard metrics can “gamify” the job, providing employees with real-time feedback and turning mundane tasks into more engaging and rewarding experiences.
Moreover, automation solutions like Rapyuta’s can help reduce costly errors such as mispicks and misshipments while boosting productivity and throughput with fewer workers. This doesn’t just improve efficiency but also makes the job more manageable, reducing the pressure on workers and helping to prevent burnout.
In conclusion, while hiring and retaining warehouse workers is undeniably challenging, innovations like PA-AMRs offer a glimpse into a future where warehouse work is safer, more engaging, and ultimately more satisfying for employees. As we continue to adopt these technologies and embrace empathetic leadership, we can create a more positive and sustainable work environment for all.