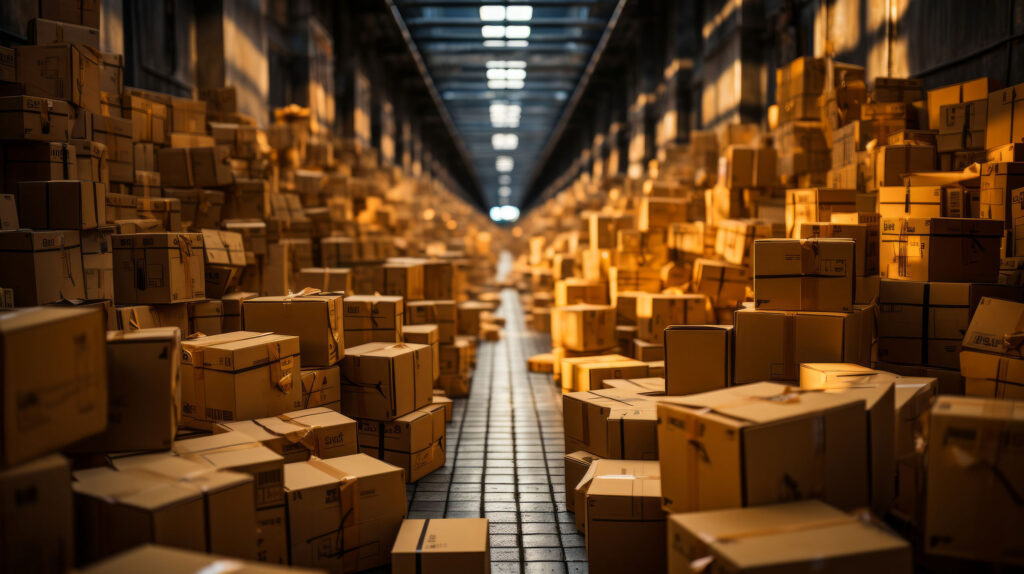
It’s beginning to look a lot like peak season …
Yes, it’s only early summer, but anyone in warehousing knows that peak season is always right around the corner and it’s never too early to start planning.
Introduction
So just how peak is peak season? In 2023, during the busiest hour of Cyber Monday, Americans spent $15.7 million per minute. And of the top 50 best selling days of the year, 45 were in Q4. In total, Americans spent $12.4 billion in the time between Thanksgiving and Cyber Monday and according to Forbes, in 2024, ecommerce sales are expected to grow 8.8 percent. And peak season isn’t just Q4 anymore, early access sales in September and October will tempt holiday shoppers to buy even earlier.
Planning for peak season has become more complicated than ever so while you still have time, consider these four things today.
1. Do Some Demand Planning to Ensure Realistic Scalability
During peak season, most warehouses need to scale up their operations profoundly to meet increased demand. A common consequence of poor demand planning is the inability to properly manage inventory, which can lead to stockouts, late delivery, higher costs associated with returns and ultimately, disappointed customers.
It’s always a good idea to review your past peak seasons in your WMS to see if your demand planning was on target and if you had the inventory you needed for increased demand. Use the historical data and algorithms for replenishment and re-order levels to help you avoid inevitable backlogs.
Higher order volume often leads to mispicks and shipping delays as well, so having the right amount of items in the right place can make a huge difference. AMRs help with inventory management tasks such as cycle counting and stock replenishment and are often equipped with cameras and sensors that can scan shelves and update inventory levels in real-time, ensuring that stock levels are accurately maintained to meet customer demand.
Our Put-to-Light (mispicking prevention) function is an assistive function that uses LED lights mounted on the trays of Rapyuta PA-AMR illuminate to show the correct position for the picked item, which reduces mispicks and improves productivity.
2. Develop a Strategy for Efficient Materials Handling and Flexible Fulfillment
Maybe you’ve enjoyed impressive shipping, fulfillment, customer service, and safety numbers throughout the years, but don’t make the mistake of thinking you can just scale up your existing workflow as-is and retain those high numbers during peak season.
It’s likely that you may need to reassess storage options and your warehouse layout. For example, maybe it made sense to store winter accessories in the recesses of your shelves, but if trends show that many more Americans will be skiing and enjoying outdoor adventures, those winter items need to be moved up stat, while lawn equipment and hammocks need to make way.
Since they can be programmed to prioritize certain areas or tasks, AMRs can adapt to changing demand patterns quickly, ensuring that critical orders are fulfilled promptly during peak seasons. And since AMRs can transport goods between different areas of the warehouse autonomously, this reduces the time and labor required for manual material handling tasks, such as moving items from storage to packing stations.
You might want to consider automated picking systems where robots are equipped with grippers or suction cups to pick items from storage bins or shelves and deliver them to packing stations. Equipped with barcode scanners and/or RFID readers to identify and sort packages, robotic sortation systems can sort and route packages based on destination during peak season, so you can ship those skis to Hawaii before the next town over.
During peak seasons, a reassessment of your workflow and layout will help you program AMRs to optimize the flow of goods by transporting items between storage locations, packing stations, and shipping areas, reducing congestion and ensuring that orders are processed quickly and accurately.
3. Use AI to Collect Dynamic, Real-Time Data
Perception is everything—an accurate understanding of the surrounding environment is what enables an AMR to make intelligent decisions. Equipped with sensors and onboard computers that collect data as they move through the warehouse, AMRs can identify bottlenecks, optimize workflows, and improve overall warehouse efficiency, which is exactly what you need during peak season.
The learning curve for robots is a lot less steep than it is for humans, so if your warehouse undergoes intensive restructuring to address peak season volatility, AMRs are agile enough to handle a wide variety of uncertainties and potential obstacles, whether it’s new floor patterns, an influx of workers, or even other robots. It’s a good idea to utilize AI-driven software that can optimize warehouse layouts, plan efficient picking routes, and dynamically allocate resources based on demand fluctuations.
By leveraging data analytics and machine learning algorithms, warehouses can adapt quickly to changing demand patterns and maximize operational efficiency. Automating order picking can reduce labor requirements by 66 percent, while also improving order fulfillment accuracy.
In 2021, Rapyuta beat out 235 global teams to win the Intel OpenCV AI Competition award for our specialized spatial AI vision systems and novel algorithms designed to work in challenging and dynamic environments.
4. Don’t Forget Your Associates
While robots are a wonderful addition to warehousing, they haven’t and most likely won’t replace living, breathing humans. Unlike robots, humans can’t operate 24/7, they can’t learn new skills instantly, and they experience fatigue and low morale after pushing themselves too hard, which can lead to mistakes and injury.
With more inventory and a compressed timeline for fulfilling orders, many warehouses hire more workers during peak season, but it’s not like skilled workers grow on trees. The days of assembly lines are long past, so the current challenge is finding skilled workers to bridge the gap between the old ways of doing things and the modern, automated warehousing landscape.
Since Covid, finding workers, especially during the holidays, is challenging. You probably don’t want to hire more FT staff since it will leave you with too many workers post peak season, but hiring temp workers also comes with problems. Often they need extensive training, especially in more high-risk, technical positions.
One solution is to train your existing workers to take on more skilled jobs—this “promotion” is an ideal way to show appreciation for your loyal workers, motivating them to stay with you in the future. It’s also a huge bonus to keep on the associates that you know and trust. No one wants a brand new forklift operator getting his/her chops up to speed at such a critical time.
Keep in mind that our universal design in picking stations enables new associates to learn the operations in the first hour, even those unfamiliar with automation equipment. Learn more here >>
Increased picking is stressful during peak season so it’s important for managers and associates to be aware of the symptoms of burnout. It may be tempting for managers to approve all overtime requests or push workers harder to meet demand, but short term gains often come with drawbacks. Retaining current and temporary associates could help you in the longer run.
When things are busy and there is more money to be made, the wellbeing of workers can move to the bottom of the list of priorities. Be sure to keep in mind that peak season is a marathon, not a sprint, and the last thing you need is for people to quit or get injured.
Conclusion
But remember, during peak season, things aren’t always black and white. While Americans spend heavily and lavishly during the holidays, there are always other factors to consider. As of Q4 2023, Americans’ total credit card debt was $1.129 trillion—the highest since the New York Fed began tracking in 1999. Will inflation, rising unemployment, and credit card debt lead to lower spending? It’s anyone’s guess, but remember to consider all factors when scaling up for peak season fulfillment.