AMR導入後、短期間での生産性アップを実現!
協働ロボットがもたらす、3PL倉庫の省人化&省力化
物流倉庫の改善を目指して協働ロボットの導入を検討されている企業担当の方々にとって、実際に導入を進めている企業の事例はとても参考になります。今回は実際のAMR導入事例について、インタビューを交えて「AMR導入のホントのところ」をご紹介していきます。
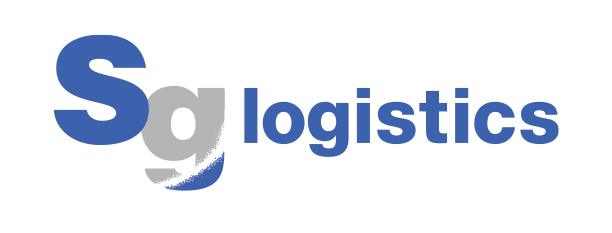
佐川グローバルロジスティクス株式会社
業種:3PL
スタッフ数:11名/日
AMR導入台数:11台
AMR稼働日:2020年8月~
導入形態:サブスクリプション(月額利用型)
今回ご紹介する事例は、佐川グローバルロジスティクス(以下SGL)。SGホールディングスグループの中で、ロジスティクスに関するコンサルティングやプラットフォーム物流などを手掛けている、3PL(Third Party Logistics サード・パーティ・ロジスティクス)企業です。
千葉県柏市にある大きな拠点の中で、BtoB向け商材の商品出荷を管理する物流倉庫内に導入されました。導入した協働ロボットは、ラピュタロボティクス社の国産ピッキングロボットを11台。2020年の8月から、倉庫内で本格稼働しています。導入前の背景から導入後のリアルな状況まで、Q&Aの形でご紹介していきます。お話を伺ったのは、AMR導入の検討段階からかかわってきたおふたりです。
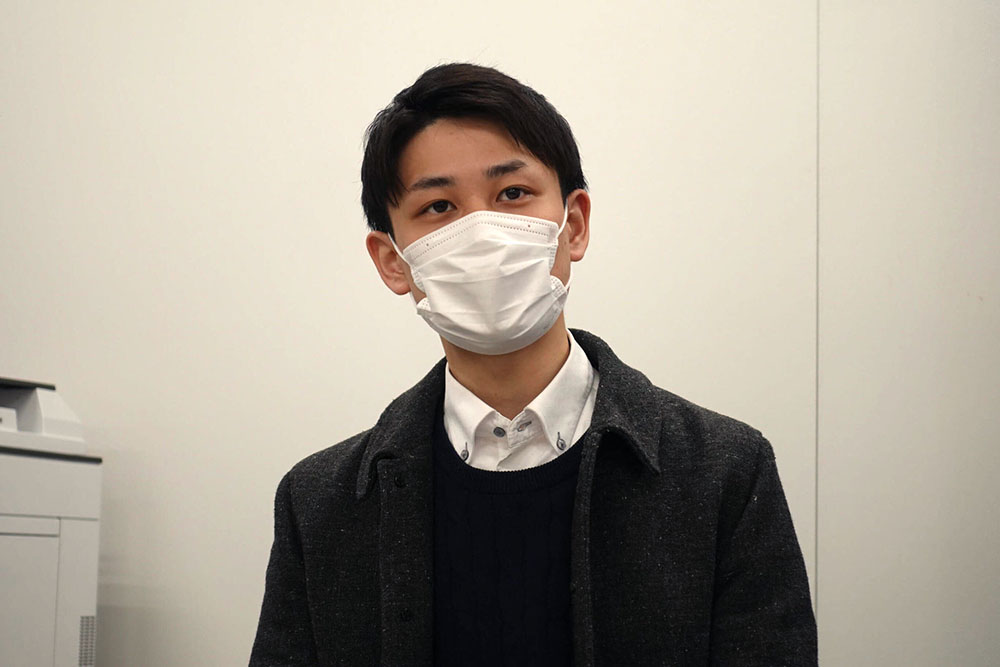
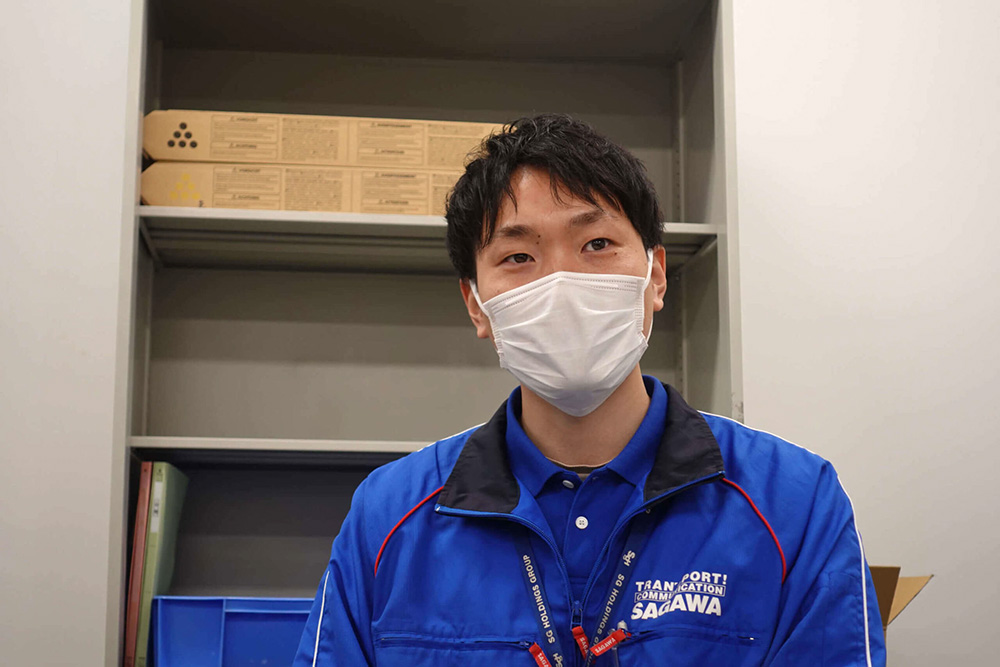
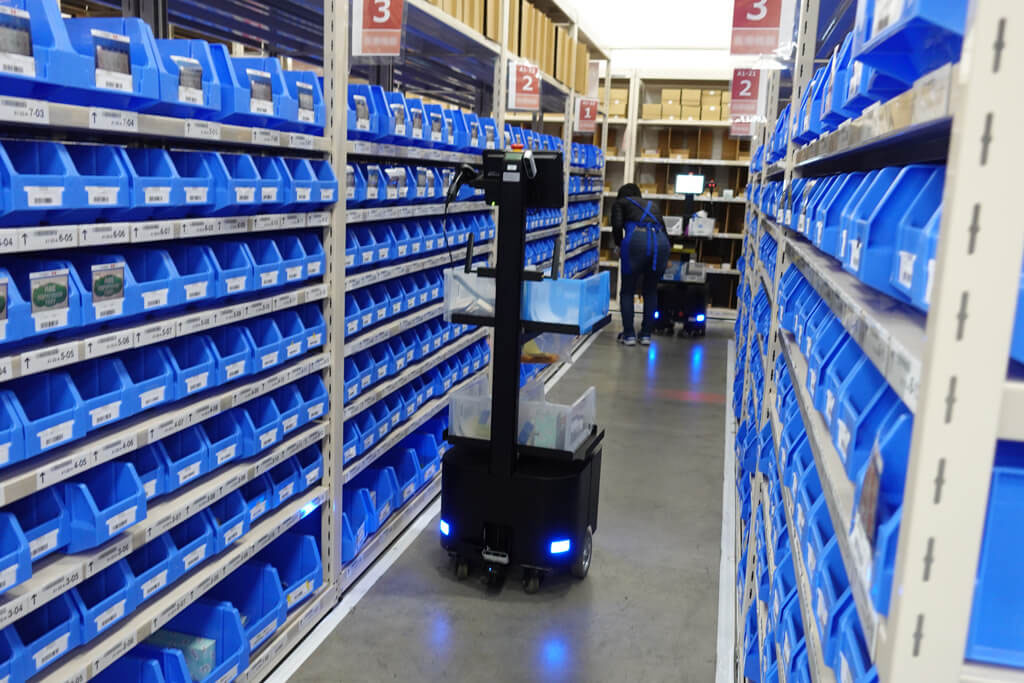
Q. 物流ロボット(AMR)導入に至った背景を教えてください。
1. 労働力不足を解決したい
「日本全体で労働力が少なくなってきている中で、倉庫内で日々行われる物流業務を自動化、ロボット化していくことで、効率化、省人化を図っていき、将来の人手不足のリスクに備えることが、大きなミッションでした」(大谷さん)
2. 長時間労働、負荷を減らしたい
「2つ目は、作業そのものの負荷を軽減したい、という課題がありました。やはり人手不足に陥ると、どうしても現場のスタッフに負担がかかります。できるだけ長期間、弊社で働いていただきたいという思いも導入の大きな動機になりました」(大谷さん)
3. ロボットとのオペレーション事例を作りたい
「3つ目は、我々SGLとしても、新しい技術を取り入れたかったというところです。人とロボット、融合したオペレーションを取り入れていくことで、これから先、そういったオペレーションが広がっていくと思っていますので、まずそういった事例をつくっていくというところでも、柏SRCに導入させていただきました」(大谷さん)
Q. 導入背景に関して、最低賃金が年々上がっていることは影響していますか?
「この柏の拠点に関しては、周辺地域での雇用単価が年々上がってきていて、繁忙期に人手を厚くしたくても、人が集まらない事態が発生しています。最終的に価格勝負になってしまうと、継続的な事業拡大が先々難しくなってきてしまうので、倉庫内の一部でもロボット化して、リスクを軽減できれば…というのは営業所のひとつの狙いとしてありました」(大谷さん)
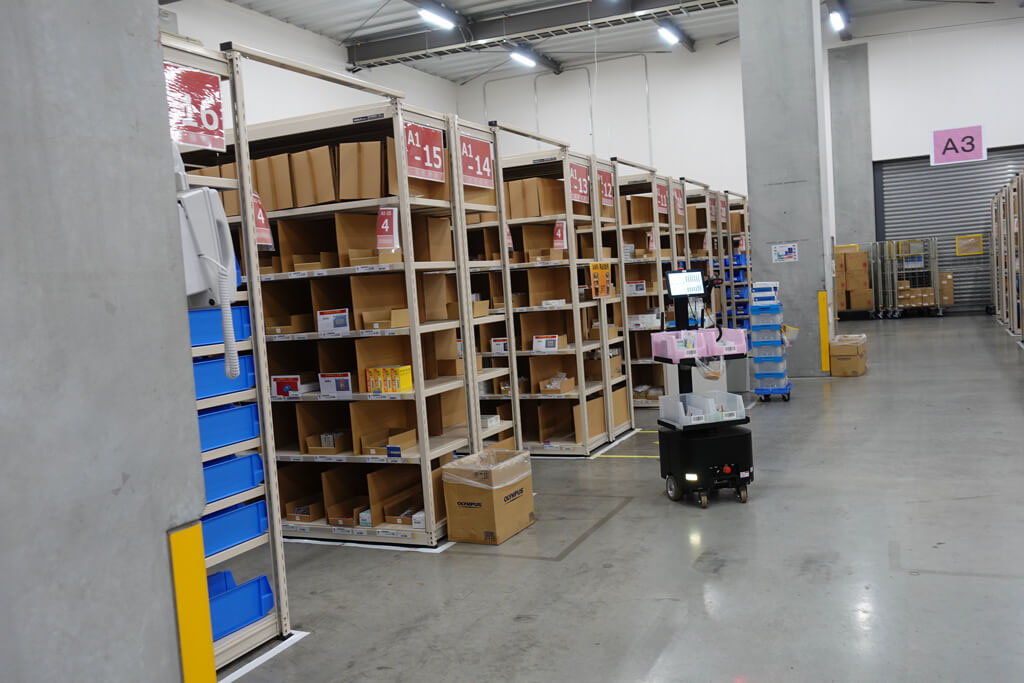
Q. 導入検討の経緯を教えてください
「検討は2018年で、ラピュタロボティクス(以下、RR)の担当の方とお話をしていて、まずは実証実験を行ってみましょう、とその時にはお話していました。実証実験が実現したのは、2019年の春頃ですね」(大谷さん)
「実証実験では、歩数や作業時間を計測して、AMRと協働したときと比較して測っていたのです。すでにこの時点で50~60%の効率アップ(作業時間の短縮効果)が見られたので、まずは、一定の効果は見込めそうだなという印象でした。もう少し細部を詰めていけば、さらにブラッシュアップできる部分も期待できそうだ、と考えていましたね」(若松さん)
Q. ラピュタ以外に検討していたベンダーは何社ほどですか?また最終的にRR導入を決めた理由を教えてください。
「ラピュタさん含めて、当時検討したのは3社ほどでした。
決定の決め手は3つあります。1番目は、ラピュタさん自身でソフトウェアを開発されているところ。我々の要望や要件にも柔軟に対応してくれたことが大きかったです。
2つ目は提案がしっかりしていたこと。
他に提案にこられたベンダーさんもいたのですが、こちらから詳細な条件を付け加えての再度の提案をお願いしても、思うようなレスポンスがなかったです。ラピュタさんは、早い段階から、細かくコミュニケーションをとっていただけたので、そこも安心できる要素が大きかったです。
3つ目は、2018年当時は協働ロボットの選択肢がそれほど多くなく、中国の倉庫をメインで手掛けているけど、日本国内の進出事例がほとんどない、というベンダーさんも多かったです。ラピュタさんはスタートから日本国内を見据えて設計していて、なにより日本の倉庫での実績が多かったので、より現実的だと感じました。加えて、スタッフさんも日本の倉庫をよく知る経験者が多かった、というのも安心できた点でした」(大谷さん)
Q. 中国だけで展開していて日本未展開のベンダーさんへの不安、というのは、具体的にはどのようなところだったのでしょうか?
「そのようなベンダーさんのロボットの実機スペックは見る限りだと、特に大き目のサイズなのが難しいなと感じていました。日本国内でよくある細い通路が入り組んだ、狭い倉庫に対応できないのではないか…と疑問に思えるところがありました。中国の巨大な物流倉庫だと、大きな通路幅だったりするので、一回に大きな物流量を意識してつくられているのだなと感じていました。そこがラピュタのAMRだと、コンパクトで小回りがききやすいものになっているかと思い、サイズ面での心配はないなと当時は感じていました」
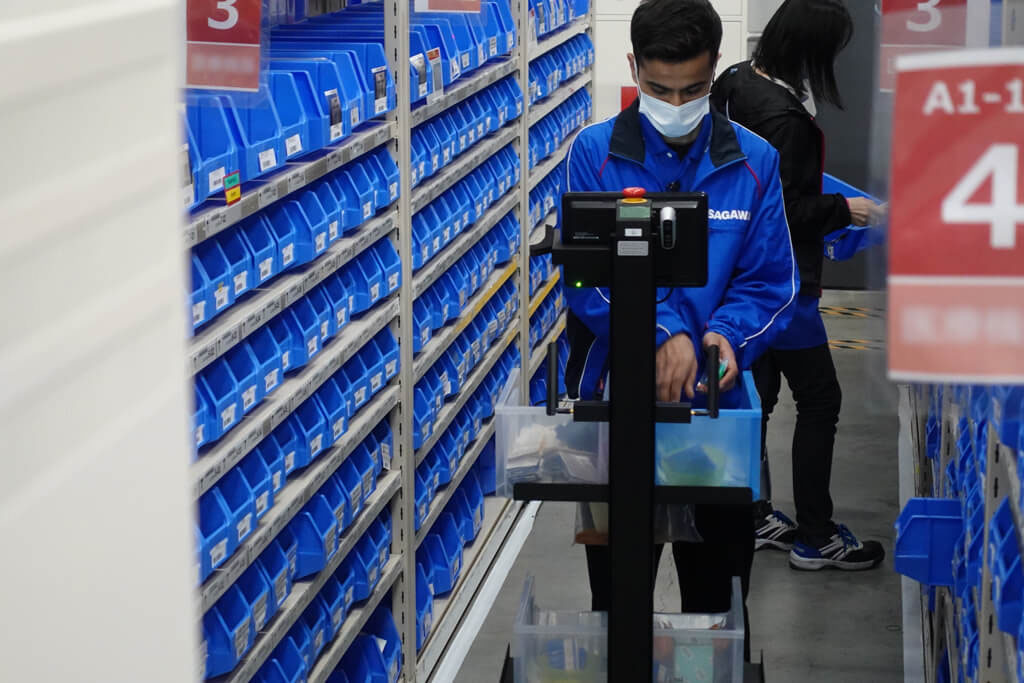
Q. 実証実験での現場スタッフのみなさんの感想はどのようなものでしたか?
「現場スタッフは社員含め、もちろんはじめての体験だったのですが、全員楽しんでやっていたというのが第一印象でした。ピッキングは、ハンディを持ち歩いて人力で行うという固定概念があったと思いますが、実験ですでに機能的に動いていたこともあり、ロボットと仕事ができて『楽しかった』というポジティブな感想が多かったと記憶しています」(若松さん)
Q. 実証実験を経て、実際に導入を決定したのはいつ頃でしたか? スケジュール感を教えてください。
「2019年の春から夏にかけて3カ月ほどの実証実験を行い、その年の秋冬で、社内稟議など、導入のための社内準備を行っていきました。やはり新たなインフラ・技術ということで慎重に討議を重ねた部分もあり、最終の承認が出るまでには少し時間がかかる部分がありました。最終的に導入にGOが出て発注したのは2020年の1月です。そこから実機を準備し、実際の導入プロジェクトは4月からはじまりました。その後、本稼働したのが8月に入ってからです。今は稼働して約半年くらいですね」(大谷さん)
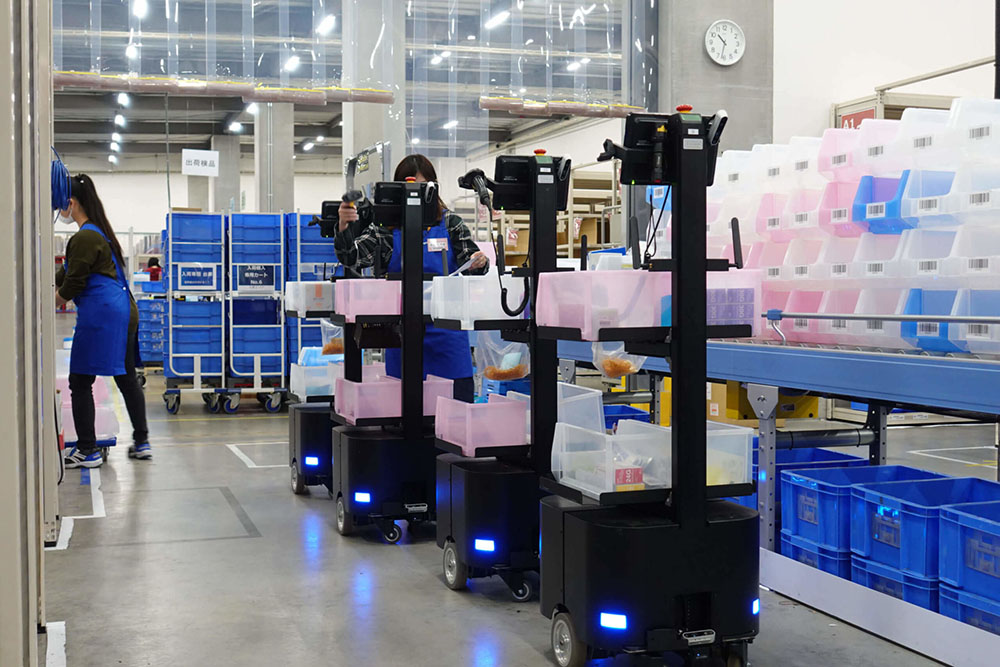
Q. 実際の導入の際に検討材料となったかと思いますが、こちらの倉庫での特殊性や、重視したポイントについてお聞かせください。
「導入した現場では、お客様からの受注の受信はほぼリアルタイムで受け付け、かなり細かい時間バッジにて引き当てをかけながら、すぐに出荷できる体制を整えて対応しています。中には、緊急出荷が必要なものもありますので、こういったことができるのが弊社の強みでもあると思っています。
そのような背景があるため庫内のリードタイムが一番の課題でしたし、ロボットを導入してもそのクオリティは必ず維持したいと認識していました。導入後は、その条件の実現ができてきていると考えています」(若松さん)
Q. そんな中、実証実験前にシミュレーションを行ったと伺っています。どのようなものだったのでしょうか?
「リアルな作業環境、実際の現場のマッピングにあわせたシミュレーションでした。その中で、人数とロボットの台数を変えたりして、複数の条件で精緻な数字を比較できたました。そのことが確認の意味でも、上申する際にも、根拠・材料のひとつになったので、とても助かりました」(大谷)
同社のシミュレーションに関しては、ラピュタロボティクスの導入を担当した小堀貴之さんにも詳細を伺いました。
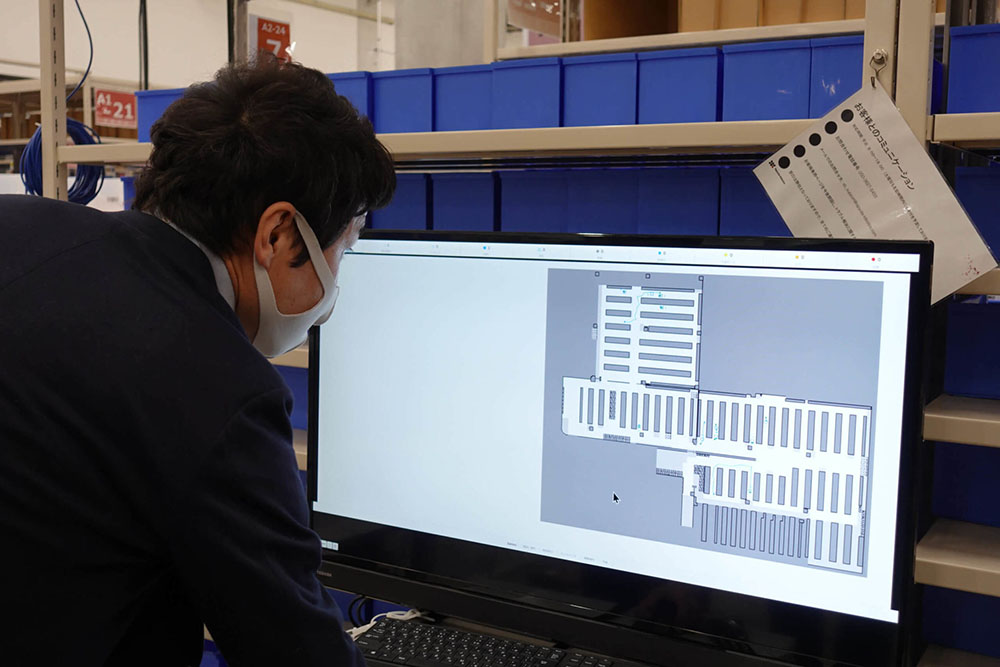
「SGLさま向けには大きく2種類のシミュレーションをご提供しました。1つ目は、単純にロボットと作業者さん何人の組み合わせでいくと、作業者さんの生産性が、どれくらのキャパがでるかのシミュレーションです。
もう1つが、現場で頻繁に起こる状況変化に耐えられるかの即応性を見るためのシミュレーションです。これは例えば、オーダーがリアルタイムに近いかたちで、バンバン入ってくるこの現場で、ピッキング途中でも、もっと早く優先的にピッキングしなくてはいけないものがあとから入ってきたらどう動けるか、そのあとをどうフォローするのか…というような、複雑かつ実践的なシミュレーションです。若松さんはじめ、現場のリーダーの方々がもっとも気にされていたことだったのですが、これを事前にシミュレーションでお示しできて、ご理解をいただいたのは非常に大きなことだったと感じています」(小堀さん)
Q. 当時のシミュレーションと、現在のパフォーマンスの間にどのくらいのギャップがありましたか?
「シミュレーションといまやっている内容だとでは、大幅な乖離はなかったのかなと感じています。最初ははじめてだったので、若干シミュレーションの数値には追いつかない部分はありましたが、半年経った今では、それらしい数値にはできていて。就業時間とか、午前便の処理量などは、近しいものになっているのが、いまの実情ですね」(大谷さん)
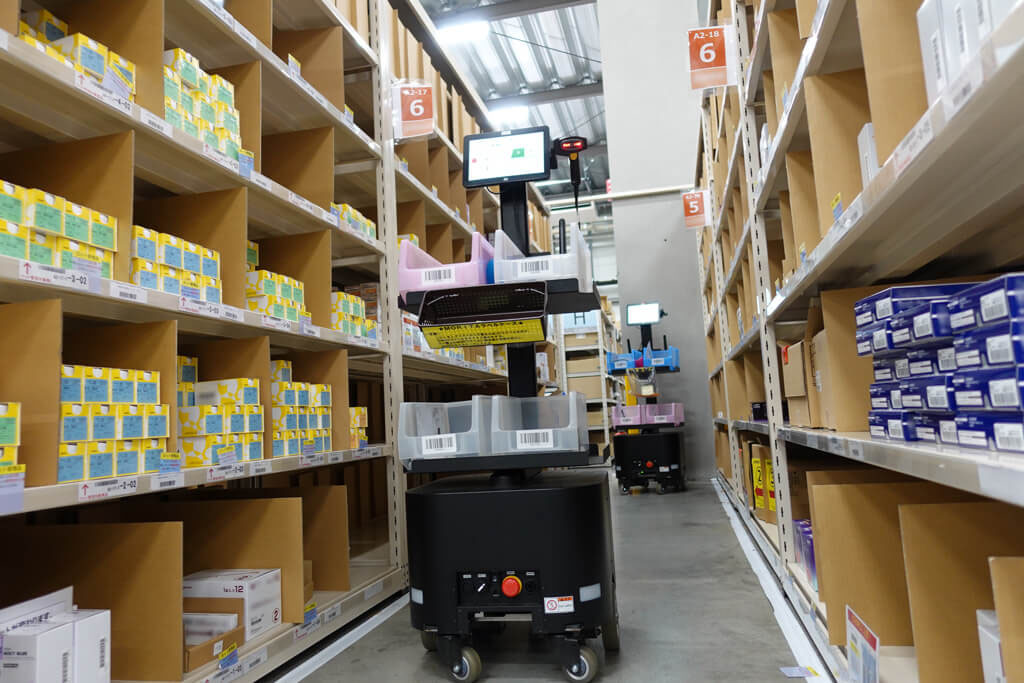
Q. AMR導入前に行った環境整備などはありましたか?
「棚幅は、当初から基準通りの90cmで設定していて、AMRと人がすれ違える幅でした。ただ、商品の棚配置はゾーンごとで調整を常に行っています。たとえばエリアに置いた商品AとBがあって、そこに通じる通路に何台もAMRが集中して渋滞してしまうことがあります。人間だけの場合は単純に在庫を集中させておいたほうが効率的だったのですが、ロボットは集まると渋滞してしまう。そのため、ある程度目安を作って商品のゾーンを分散し、バランスを見て配置しています。ここはAランク品のゾーン、反対側はBランク品、といったような調整ですね」(若松さん)
Q. AMRを運用する中で、実際に結果としてどのような成果が出てきていますか?
「実態として、時間あたりの処理量が凄まじくあがっています。例えばシステムトラブルなどで、今日はロボットが動かせないという日があると、進捗が全然違います。たった1~2時間でも明らかに影響が大きいなと感じますね。『すぐに2~3個の出荷を処理したい』みたいな瞬発力を要する出荷作業だと、人間がハンディをもって処理するほうがいいのですが、1日通しての作業を時間あたりで見ていくと、まったく違います。AMRが止まったとたん、進捗が目に見えて悪くなるのは実感するようになりました。
数字でいえば、導入前後の生産性だけの比較では、現状ですでに2倍には到達していますね。処理量としては、ハンディのみの時と、AMR導入後での大きく違いがでてきています」(若松さん)
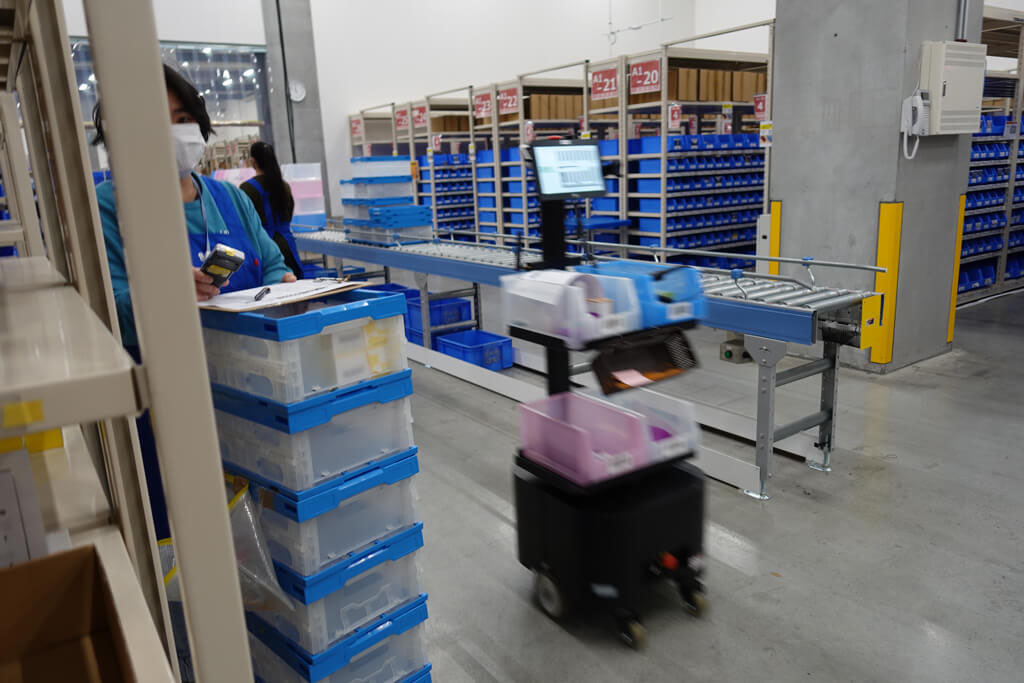
Q. 倉庫内を拝見すると、人力でカートを押してハンディのみで作業している部分も、いまだにミックスされているかと思います。すべての作業をAMRに任せていない理由を教えてください。
「まず出荷商品の容積的な問題というのがあります。ラピュタのAMRだと、積載できる容量限界の問題があるので、大きな商品などは人間が行わねばなりません。
あとは効率的な問題もあります。
先ほどもお話したように、たとえば明細が1行・1店舗のときとかは、人間がハンディでサッと取りに行ったほうが瞬発力はありますね。AMRで行くと積付け、積み下ろしが絡んでくるので、前後に時間がかえってかかります。
明細の条件によってAMRを活かせないパターンも当然あるので、そこは、適材適所で、容積が多いものなどはハンディ側に振り分けてデータを送っている、という形で活用しています」(若松さん)
Q. そういったデータの振り分けはどのようにコントロールされているのですか?
「WMS(Warehouse Management System:倉庫管理システム)に飛んできた引き当てデータをみて(SGLの)社員が振り分けをしてラピュタのシステムに送っています。今日どういう進捗だから、今日こうしなきゃいけない、
ネタがすくないから、ロボットに振り分ける、など、現場の社員がコントロールしています」(若松さん)
Q. そのほかに、導入後の運用で工夫した部分はありますか?
「導入後に、現場スタッフの動作をラピュタさんが分析してくれたのですが、『人がロボットを探す』というのが、動作分析でかなり見えてきました。
ロボットを探している時間を減らすにはどうしようかと考え、現場の意見を聞いて、天井に照射するLEDライトをつけてAMRの大まかな位置把握をするといった工夫を試していますね。AMRがもともと発している音と合わせて、場所を把握して動いています。」(若松さん)
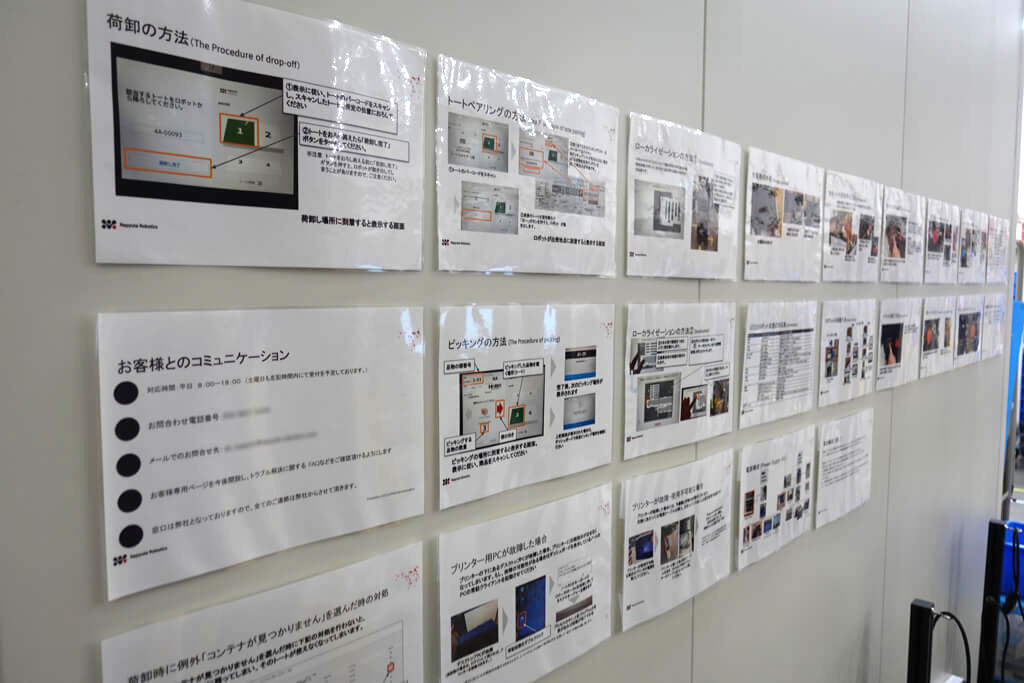
Q. 導入後の現場スタッフの方の、リアルな声をお聞かせください。
「ロボットがピッキングする棚のところに止まって、スタッフを待つので、最初の頃は、カートで手動ピッキングしているスタッフが『邪魔だ!』と思ったりしていたみたいです(笑)。これも人間とロボットが協働する上では、よくある話だと思っていたのですがやっぱりこうなるか…とは思ったことがあります。
ですが「ロボットと共に」というマインドをスタッフ間で共有して大事にすることで、そういった声もすぐに上がらなくなりましたし、自ら『どうやってやるの?』と聞いてくるスタッフも増えてきました。また合わせてひんぱんに研修などを行い、ロボットを身近にさせたことというのが、現場サイドからおこなったことではありますね」(若松さん)
Q. スタッフへの研修はどういった内容だったのですか?
「難しいことはせず、単純に“まずは触れなさい”というところから始めましたね。
操作マニュアルなどはラピュタさんに作っていただいたものもあり、活用していましたが、とにかくロボットに触ってもらうところから研修を行いました。実際にやってもらって、ロボットと協働することを、自分事として捉えてもらった、というのはとても良かったと思います。その結果、半年経った今ではもう現場には違和感がほぼないですね。「邪魔だよ」なんて、誰も言いませんし(笑)、お互いが共存してピッキングしていると感じていますね」(若松さん)
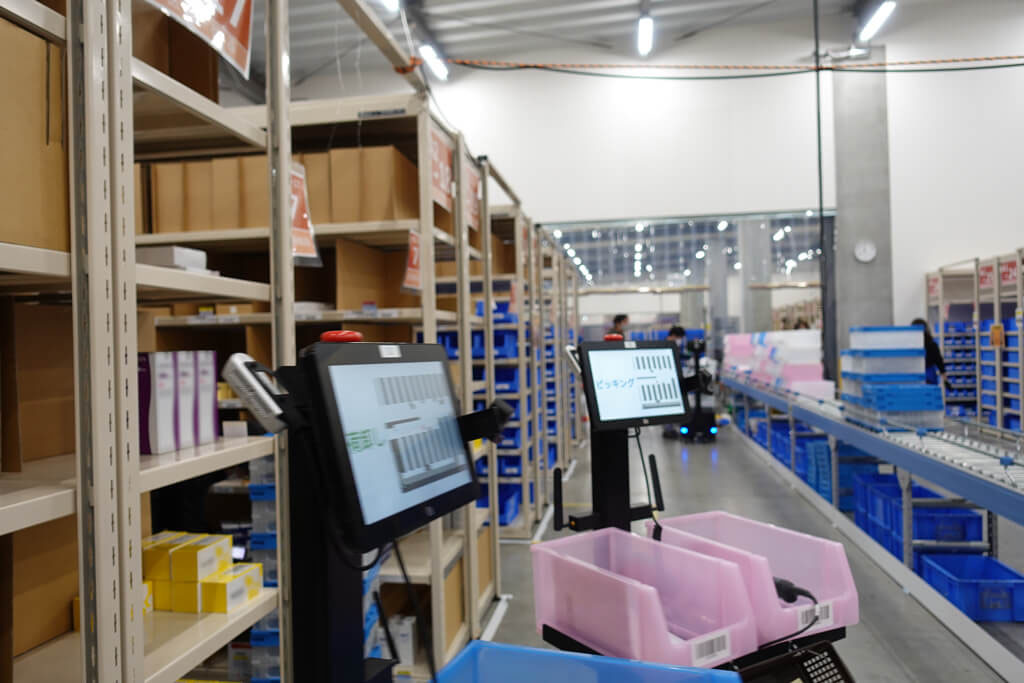
Q. 当初のターゲットにしていた、費用対効果は出ているでしょうか?
「半年たった先月、目標値の約7割程度の効果になりました。半年なので、まあ順当かなと個人的には思っているのですが、さらなる改善を望んでいます」(若松さん)
Q. 今後のSGL内での展開予定を教えてください。
「ここのオペレーションセンターで言えば、適した商材のエリアなどのパターンを、まだ細かく精査しているところです。ただ、ここで徐々に実績が出てきたので、その導入&運用情報をもとに、全国各地の営業所へ導入ができるかを徐々に検討を進めているところです」(大谷さん)
Q. ここの1拠点でさらに増やす、というよりは、同じ形のソリュ-ションを別の拠点に増やしていくということですね。そのぐらいインパクトが大きかったと?
「そうですね。SGLのオペレーション方法にマッチしている部分があります。完全な機械化、というよりは、半分が人、半分がロボットで、緊急時もこれまで通りの人のみの運用に戻せるので、リスク管理もできる。そこが3PL業者である我々にとっても適しているなと感じています」
まとめ
導入時の条件設定について聞いたほかのお話だと、SGLの持つ倉庫の床の耐荷重が、そこまで大きくない倉庫もいくつかあるそうです。そういったところに大型のインフラ投資を行うのがますます難しかったのだそうです。中規模の物流現場を数多く保有する倉庫には、そもそもAMRに適正がある、ということがあるかもしれません。
またもうひとつは、シーズン、週内、時間、などで“波動”の大きい物流倉庫に、固定型の大型システムやロボットを導入してしまうと、それが結果として現場でボトルネックになる可能性があるということ。
SGLの導入例のように、AMRであれば、ある程度の波動も現場の対応力で吸収でき、仮にAMRで処理できないほどの出荷数量がきたときには、人が作業すればAMRの処理能力の不足分を補えるのです。
こうした現場の実例からも、AMRのフレキシビリティの高さが使いやすさにつながっていることが見えますね。
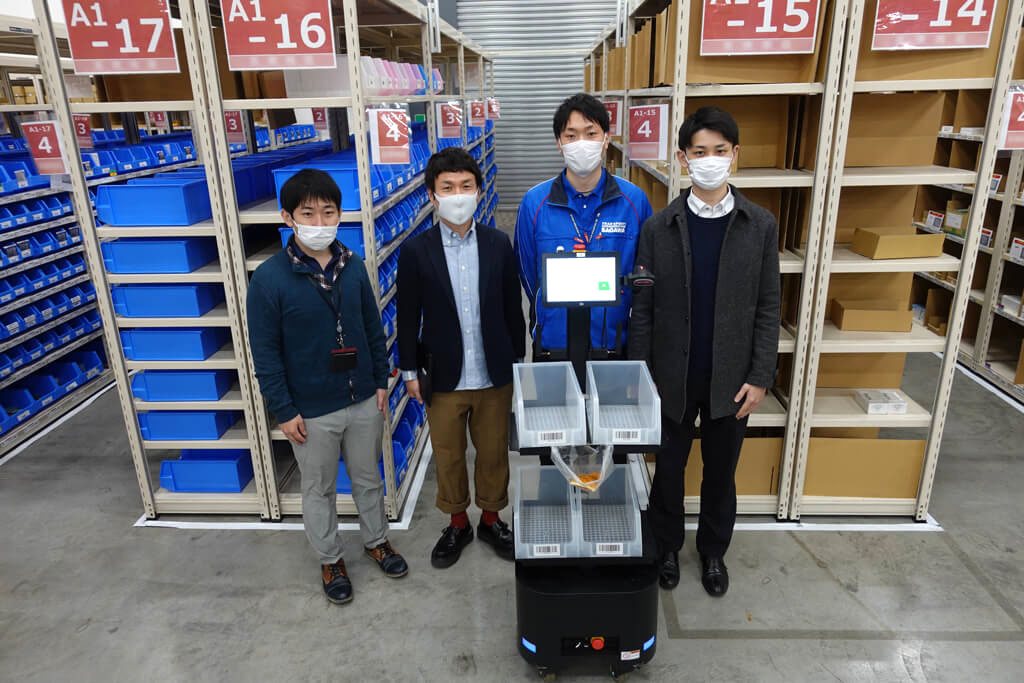