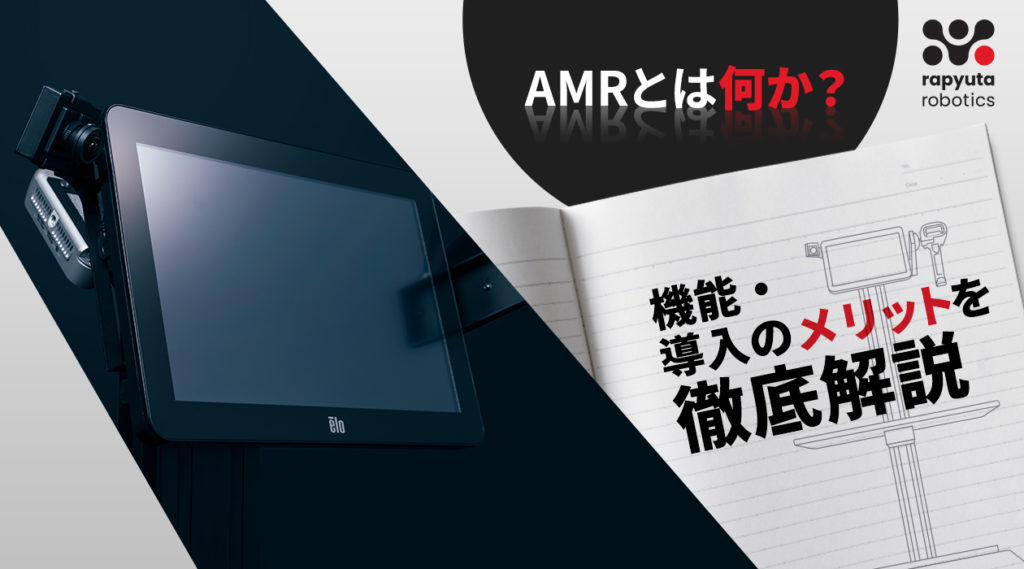
慢性的な人手不足は現在の物流業界の抱える大きな課題です。その現実的な解決策として脚光を浴びているのが、自律走行できる協働ロボット「AMR」です。物流倉庫でのピッキング業務を効率化・省力化するためのカギとなるAMRについて詳しく解説していきます。
◾️AMRとは何か
AMRとは、Autonomous Mobile Robotの略称で、日本語にすると「自律走行搬送ロボット」となります。
AMRの活躍の場は、おもに倉庫内での「ピッキング」がメイン。ピッキングするスタッフの作業をアシストする形で活躍するため「協働ロボット」とも呼ばれています。
AMRの特徴は、磁気テープによるコースガイドなどの誘導を必要とせず、群制御AIによって適切なルートを算出し、完全自動で走行します。
例えばピッキングでは、AMRが指定されたロケーションに向かって自動で走行し、人(ピッカー)が商品をピックアップし、バーコードをスキャン、そして検品を行います。これをAMRが積載するコンテナ(通い箱)などで受け取り、ピッキングが終わると出荷作業をする場所まで自動で運ぶという流れで動きます。
現在、AMRとオペレーションシステムを国産で製造・販売するメーカーはまだ多くなく、日本国内ではラピュタロボティクスが唯一の国内メーカーとして、製造、販売と月額でのリースにも対応しています。
◾️AMR導入のメリット
倉庫の条件があえば、AMRの導入にはメリットがとても多いです。
もっとも大きな部分は、生産効率性アップの面です。従来は人がピッキングして次のロケまでカートを押して移動し、遠い集荷場所までカートを押していって、荷降ろしをする…という流れでした。またピッキング作業は人手に頼らざるを得ない部分が多くあり、自動化が難しい領域でもありました。
そこで、ピッカーが現在行っているオペレーションは大きく変えずに、ピッカーはピッキングに専念。AMRは運搬と検品スキャン、ロケーション指示を担うことで、働くスタッフの生産性向上と労働環境の改善を同時に実現しました。
人手不足と、働き方改革への対応を迫られる物流企業にとっても、問題を一挙に解決できるのです。
ハードとしての性能面も優秀です。通路幅が狭いような中小規模の倉庫でも動けるよう、機動性が高いデザインで作られています。たとえばほかの作業者の邪魔にならないように避けて走行したり、仕事が終わると所定の荷下ろし場所に戻る、作業する人間との協調性を重視した動きができるのも特長です。
また積載できるコンテナ(通い箱)も、大きなものから小さなものまで柔軟に対応できるため、多様な大きさの商品をピッキングする通販倉庫などにもマッチしており、積極的に導入が進んでいます。
さらに、倉庫内の在庫情報から帳票類の発行までを一元的に管理するために倉庫に導入されている、WMSやWESと情報を連携して運用します。既存のインフラの中にAMRを融合させることで、初期の導入障壁は格段に低くなります。
これらの特長を総合すると、投資対効果が高くなるという点にも注目です。導入にあたっては、倉庫内のレイアウト変更を行わずに導入ができるので、導入費用を抑えて、効率の最大化を現実的な範囲で目指すことができます。さらにリースでの導入が可能で、繁忙期には台数を増やすことができるので商戦ごとの波動対応もスムーズです。
◾️AMRが物流業界全体の課題解決を担う
日本において、労働人口は今後減少していくことが明確です。人的リソースの減少は物流業界にとって大きな問題であり、一刻も早く対処していかなくてはなりません。自動化やロボット化は、遠い未来の話でもなく、大企業だけが手掛けることでもありません。
ただ現実問題として、既存倉庫での大掛かりなロボット導入は、設備全体の入れ替えを求められ、一時的な多額投資と現状のオペレーションを止める検討を必要としてしまいます。
そんな中、AMRは既存倉庫にフィットする現実的な選択肢として注目されています。数台からでも簡単に導入ができるうえ、すでに日本各地の中規模倉庫で確実な実績も積み上げています。
初期投資を抑えながら、徐々に自動化にシフトしていきたいという倉庫にとって、AMRはまさにうってつけのチョイスだと言えます。
必要に迫られている自社のDX化推進と、省人化、省力化による効率アップは、AMRで一挙に実現できるのです。