Keiyo Distribution Warehouse Co., Ltd. was founded in 1966. The company’s business includes the warehousing and storage of a general line of goods that support the retail industry. In this case study, Keiyo reveals the secret to increasing productivity by picking with collaborative robots.
For companies considering the use of collaborative robots to improve their logistics warehouses, case studies of companies that have introduced such robots are helpful. We interviewed the key personnel responsible for integrating AMRs to share actual experiences of AMR introduction.
Keiyo Distribution Warehouse
Industry: 3PL
Number of staff: 100 people/day
Number of AMRs installed: 20 (applied to some divisions; there are about 8 staff members working with AMRs)
AMR operation start date: December 2020
Introduction form: Purchase type
In this case study, we introduce Keiyo Distribution Warehouse Co., Ltd., which has many distribution warehouses throughout the Kanto region in Japan. Keiyo is involved in 3PL (Third Party Logistics) in a wide range of fields, from logistics operations for the manufacturing industry to distribution logistics for supermarkets and convenience stores. In addition to AMRs, the company is actively promoting DX by adopting weighing carts, motorized mobile shelving, and other complex systems. We interviewed Mr. Yuichi Iizuka, Executive Officer and General Manager of the DX Promotion Office, who oversees the strategy at the center of the company. We asked him to share the details of their AMR introduction, from consideration through integration and building cooperation with front-line staff.
The base where the collaborative robots are being introduced and operated is the Iwatsuki Warehouse in Saitama prefecture, which supplies pet supplies to nearby large supermarkets. Twenty domestic picking robots from Rapyuta Robotics have remained in full operation since December of 2020.
“Primarily due to the shortage of manpower, which is becoming more severe every year. The Saitama area where this base is located is suitable for a logistics base, and there are many competitors. As a result, it is becoming increasingly difficult to acquire human resources every year. Yet we still have to win in the local market. We decided to take the initiative to introduce on-site logistics equipment in order to save manpower and labor as quickly as possible,” stated Mr. Iizuka.
Q. Has the fact that the minimum wage is rising every year had an impact on your introduction of this system?
“Yes. The labor shortage in the logistics industry is becoming more serious in many places, but this area is fiercely competitive, as mentioned above. All of our staff members live nearby and commute by car. Kawaguchi City and Koshigaya City in the southern part of Saitama have a large population commuting to Tokyo. But the northern part of the city, bordered by Route 16, has a declining population making it more difficult to secure staff. In addition, several large warehouses are being built in the area, and the cost of acquiring staff is rising rapidly. As a result, the hourly wage rate appears to be increasing every month. However, for small and medium-sized companies like ours, it is not easy to raise the hourly rate. Against this background, we predicted that we would not be able to secure any additional workers in five years. Therefore, considering how to maintain performance with a small number of staff, we decided to introduce robots as a realistic option” Mr. Iizuka added.
Q. How did you come to consider introducing this system?
“We began considering it in 2019, before the advent of COVID-19. In the beginning, we were mainly considering GTP (Goods to Person robots), and there was little information about AMRs,” commented Mr. Iizuka “After much deliberation, we decided on the AMRs from Rapyuta Robotics in May of 2020, made preparations for its introduction, and launched its operation in December of 2020.”
Q. How many other vendors were you considering?
“Initially, we narrowed our choices to domestic vendors for GTP, but there was the issue of cost because it would be a large investment. In order to install the GTP, we had to empty the warehouse, install special shelves and electrical work, and build a fence to separate the area for the robots. Even if we were to reduce the workforce significantly, it would take a long time to recover the cost, so we canceled the project at the last minute,” Mr. Iizuka shared.
“Then, as an alternate approach, we researched collaborative robots. At that time, most of the AMRs were made in China, but they had major limitations such as not being able to support detailed customization. They were also not designed for B2B. We wanted a robot that could carry 50 liters of folding containers. Then, at a warehouse preview, we came across the AMR from Rapyuta Robotics and considered introducing it.”
Q. Why did you finally decide to install the Rapyuta AMRs?
“First, it is a domestically produced AMR with a large size, and it can be customized to carry the aforementioned 50L folding container. We asked several other manufacturers for proposals, but Rapyuta Robotics was the only one that met our requirement to accommodate 50 liters. Second,the software that allows people and robots to work together efficiently was impressive. This concept was fundamentally different from other systems we reviewed, such as “swarm control” where multiple robots work together. As a result, we concluded that the Rapyuta Robotics solution was the best way to increase productivity in a medium-sized warehouse like ours,” stated Mr. Iizuka.
Q. What were your impressions of the AMR’s software, rapyuta.io, following the preliminary simulation?
“The picking efficiency was about 130 lines per hour*. At the current site, picking is done using a four-order multi-picking cart, and there is just one fast worker who can do 140 lines per hour. We decided that we’d introduce the system if the average overall productivity matched that of manpower. Because we nearly matched the manpower output through simulations, we felt comfortable setting these as realistic targets post-introduction,” he declared.
(*The number of slips (lines) that the staff picks within a certain period of time indicates the picking efficiency. It is calculated by dividing the number of shipping data lines by the picking time.)
Q. After the implementation, what challenges did you face compared with those projected in the simulation?
“The test run was in December of 2020, and we launched full-scale operations in January of 2021. It took about six months from initial preparations to integrate the system. By then, the staff had become accustomed to the AMRs, and we were able to pick smoothly to some extent.
However, the Iwatsuki Warehouse is characterized by busy picking and shipping work in the morning. There is little lead time and the first flight leaves at noon, so we have to bring in about 100 staff members at once. During these times, it is difficult to run the AMRs because we don’t place them in areas where forklifts are moving at high speed or where there is a concentration of people. When we run them in the morning, we work in separate picking areas.
“Therefore,” Mr. Iizuka continued, “the AMRs are mainly used in the afternoon for the next day’s delivery. While we currently use human labor to pick urgent items, our goal is to incorporate AMRs for this purpose as well.”
Q. It has been six months since the system was launched, how would you evaluate its performance in the field?
“We’ve begun to feel the effects,” remarked Mr. Iizuka.“ People have gotten used to the system, and, with constant tuning, the system is working better and better. The AMR’s productivity has increased. While we are n the midst of repeated improvements in the field, we hope to see results gradually.”
Q. Can you elaborate on the tuning of the system?
“Collaborative work (performance of instructions from the robot), avoiding traffic jams, driving speed in aisles, and accuracy of obstacle detection has improved. The accumulation of these improvements is having an effect. As Rapyuta continues to provide upgrades, in response to requests, expect to see increased productivity,” he suggested.
Q. What do you think will be the key to increasing productivity through collaborative work with AMRs?
“Ideally, we would like to run 20 robots with as few people as possible. If people are assigned to each area, productivity cannot be improved, even with additional robots. We found that the key to efficient AMR operation is to have a small number of staff working alongside, without breaks. If you want to finish the work quickly, you can do it with 20 robots and 20 people, but then you have to pay for 20 people. When we think of labor saving, we tend to think of operating robots without a break. But in a small warehouse, shifting to an operation with fewer people will lead to higher productivity,” analyzed Mr. Iizuki.
“When we were considering the introduction of this system, we observed that other robot manufacturers were running AMRs in zone picking. But I believe this would have a negative impact on productivity. Having people waiting on a robot would be a big loss of time, wouldn’t it?”
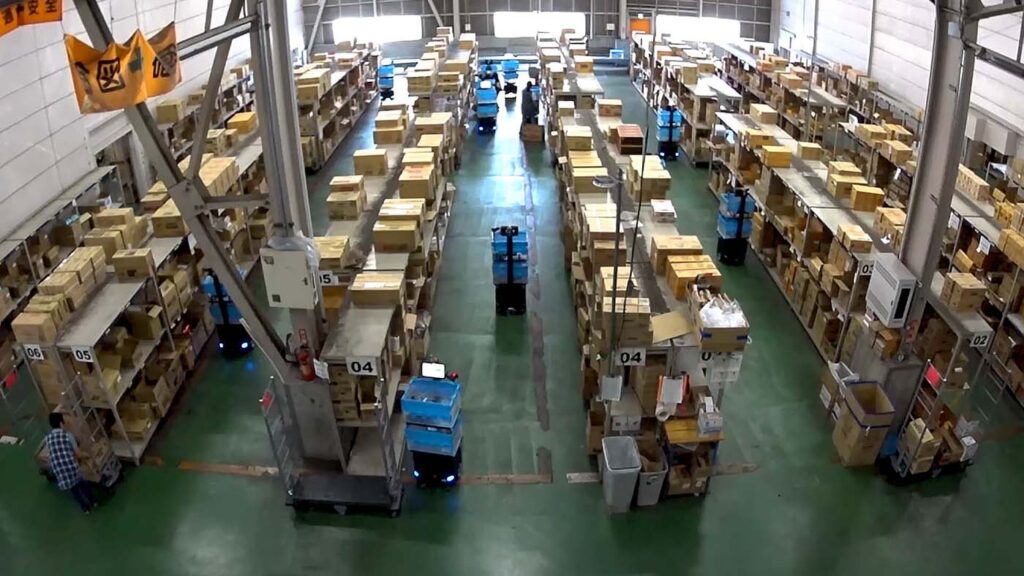
Q. What are your impressions from the field staff who worked with the robots?
“The first thing to do when working with robots is to become accustomed to their presence. Humans tend to move in one direction, but robots take the shortest route even if that means coming from the opposite direction. I was surprised by their movements at first,” laughed Mr. Iuzuki. “I got used to it once I realized that they actually avoided bumping into me.
“It took a few months to get everyone acclimated to the presence of AMRs, because there were many staff members, including short-term workers. Once they understood the robot’s characteristics, and how to move it, the movements l became smoother. They began to understand how to behave with the robot.”
Q. What is the task at hand?
“We anticipated that the movement of the AMR would be smooth if there were no obstacles, and that we would eventually reach the values of the initial simulation. However, during very busy times there were many obstacles in the warehouse which caused time loss. The aisles are wide enough to pass each other, but when there is a rush of orders to one shelf, there is a wait in front of it. If we can solve these problems, we may be able to exceed our goals.”
Q. What is your current level of productivity, and what do you aim to achieve in the future?
“We are averaging about 100 lines of productivity per hour, but we think 130 lines is now possible. The productivity of the four-order multi-picking cart (a semi-automated solution developed by Keiyo) averages about 100 lines and that was our benchmark,” he indicated.
“The AMRs are still underutilized. Initially, in order to reduce transportation costs, we were allocating orders with an emphasis on loading efficiency. But we believe that by reviewing this balance, we can optimize the waiting time for the AMRs as well as the lead time. Rapyuta Robotics is currently working on this improvement for us.”
(*Note: There may be a trade-off between increasing the loading rate of the container and shortening the flow line.)
[Summary]
This case study was a small to medium scale warehouse that supports retail distribution among 3PLs. It is a site where occasional large volume shipments are accomplished with a lot of manpower, and where quick picking is required in a small, narrow location, requiring a flexible response.
In addition, there are many fixtures, people, and forklifts in operation, and a conveyor belt that encircles the perimeter, making for a complex topographical environment. The Iwatsuki Warehouse can be described as a “standard distribution warehouse in Japan” in this regard.
Previously, it was difficult to adjust AMRs to increase production efficiency at such a site. But the solutions from Rapyuta Robotics are flexible enough to be used at these sites and contribute to improving daily productivity. Both the Rapyuta AMRs and the rapyuta.io system receive daily feedback from the shop floor to fine tune the system to achieve even higher levels of functionality.
The end result for Keiyo is a permanent solution to a severe labor shortage, and a means to improve overall warehouse productivity and efficiency.